Nuestro parque de más de 50.000 robots colaborativos vendidos y trabajando en todo el mundo se ha convertido en una valiosa fuente de información que nos ayuda a aprender, a tomar decisiones y a diseñar los servicios del futuro. Nos basamos en los datos y en lo que nos transmiten los clientes de cualquier industria.
Hoy queremos hablar de cómo las empresas (muchas de ellas pymes) que han dado el paso a la fabricación avanzada con cobots perciben la automatización y la robótica industrial, opiniones que esperamos resulten de valor si estás pensando en dar el paso para hacer crecer los resultados de tu negocio.
El factor humano en el centro de la automatización
Siempre hemos defendido que hay tareas que pueden (y deberían) automatizarse: cargar y descargar, atornillar, colocar piezas, soldar… El beneficio de robotizar estos procesos lo experimentan las empresas, con una mejora en la productividad y en la precisión. Pero también los trabajadores. En la industria 5.0 a la que nos encaminamos, los empleados pueden delegar las labores arduas y peligrosas para centrarse en las que generan más valor y requieren habilidades exclusivamente humanas, como la creatividad.
No estamos tan lejos de ese horizonte. En numerosos proyectos con clientes y colaboradores ya hemos visto que los robots colaborativos UR sacan lo mejor de los empleados humanos.
Automatización colaborativa como disparador del talento humano
Sí, automatizar la producción y aumentar la plantilla es compatible. De hecho, es un efecto que encontramos a menudo, ya que el aumento de la productividad ayuda a que las empresas locales mantengan la fabricación en el país y necesiten contratar a más personal. “Desde que instalamos el primer cobot en 2011, nuestra plantilla ha aumentado un 50% y nuestra facturación, más del 70%”, nos confesó Laurent Wagner, CEO de BWIndustrie.
En esta misma línea, Aurelio Tornero, Director General Industrial de RNB Cosméticos, explica: “nuestros empleados de siempre, que antes se dedicaban a mover materiales, están trabajando con los cobots desde el primer momento”. Y añade: “no estamos incorporando a gente muy experta para manejar un robot de última generación, sino que estamos haciendo experta a nuestra plantilla y su nivel de competencias está aumentando”.
La idea de que los cobots son un disparador del potencial humano la vemos reflejada, sobre todo, en los centros formativos. Según Jose Antonio Pérez, profesor del instituto Palau Ausit, “para los alumnos es un aliciente practicar con los diferentes robots y ver que lo que hacen en la escuela es útil en un entorno real”.
Este centro formativo fue uno de los participantes de la primera Catskills sobre robótica industrial, que se celebró en el hub de Universal Robots en Barcelona para poner a prueba a los alumnos de enseñanzas profesionales. Para Daniel Flores, director técnico del certamen y profesor de sistemas electrotécnicos y automáticos del instituto Jaume Huguet, “el cobot tiene la ventaja de que se puede programar de manera versátil y fácil. Lo vemos en las Catskills, con los proyectos que se completan en tiempos tan ajustados”.
Cobots que despiertan vocaciones
Sin salir del entorno educativo, nos podemos remontar a la feria Advanced Factories de 2019, cuando UR organizó la competición Hack the Cobot. Tres centros formativos tuvieron que manejar en directo a sus UR3 para conseguir ensamblar un teléfono móvil en varias fases. Para Gabriel Cammany, capitán del centro ganador de la prueba, La Salle Barcelona, lo más positivo de la experiencia fue “el hecho de poder trabajar con robots colaborativos de Universal Robots y de entender lo asequible que puede ser si tienes conocimientos previos. Es realmente fácil y puedes llevar a cabo cualquier reto que te propongas”.
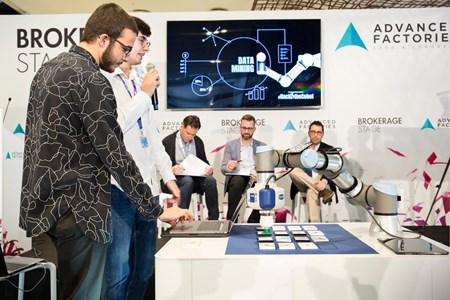
Reducir riesgos laborales con cobots
Otro beneficio de la robótica colaborativa es que reduce el riesgo de sufrir lesiones en las fábricas, tales como los trastornos musculoesqueléticos. Sobre todo cuando hablamos de tareas arriesgadas. Es algo que conoce de cerca la ingeniería Arquimea, que trabajó en un proyecto para que los brazos robóticos, colgados, trabajaran en el mantenimiento de las aspas de aerogeneradores.
“El pulido es un proceso cansado para los trabajadores que reporta bajas por problemas de esfuerzo y también por el polvo que genera. La automatización de este proceso permite minimizar riesgos laborales y una mayor calidad para la salud de los trabajadores”, considera David Álvarez, Robotic Systems Engineer de Arquimea.
Mantener el layout de planta existente, preservando la seguridad del empleado
Otra de las opiniones más extendidas acerca de la automatización y la robótica industrial con cobots es que, gracias a su baja huella y su versatilidad, pueden incorporarse en la planta de fabricación sin tener que modificar el layout previo. Para empezar, no es necesario invertir en un vallado de seguridad.
“Gracias a la estandarización, el coste de los robots y el hecho de no tener que instalar un vallado ni estaciones grandes, hemos conseguido un retorno de la inversión mucho mayor que con maquinaria industrial o robótica tradicional”, explica Daniel Llin Terol, New Technologies Engineer de Ford, cuya planta en Valencia instaló su primer brazo robótico en 2016.
Trabajo 24/7 y en multiformato
Otro motivo de mucho peso a la hora de automatizar es el de poder añadir un turno de trabajo nocturno sin tener que agregar costes de personal. De hecho, a menudo los robots colaborativos son utilizados para avanzar el trabajo más tedioso durante la noche para que los empleados puedan mantener la producción por la mañana.
Es un modo de producción 24/7 que la empresa de logística multicanal DCL Logistics incorporó tras recibir un UR10e. “Cuando los trabajadores llegan por la mañana para encender sus máquinas, se encuentran con una gran cantidad y variedad de pedidos. Siempre nos piden que encendamos el robot y lo pongamos en funcionamiento, ya que les quita un peso de encima”, cuenta Isaac Toscano, ingeniero de automatización de la compañía.
Y lo mejor de todo es que el cobot no tiene que pasar todo un turno de trabajo haciendo la misma función para sacar adelante un único lote de productos. Si la demanda es volátil y fragmentada, la tecnología industrial tiene que estar preparada, ¿verdad?
“Antes se necesitaban seis horas para pasar a un producto diferente, pero con los robots UR los cambios se realizan en tan solo 20 minutos”. Lo dice Johnny Jansson, gerente técnico de Atria, una empresa sueca de productos vegeterianos y gourmet. La compañía tan pronto etiqueta, envasa y paletiza gambas, como lo hace con aceitunas, ajo o tomates deshidratados.