Entrevista a fernando cao, director de emenasa industria
La flexibilidad de las instalaciones se ha erigido como la punta de lanza de Emenasa Industria y Automatismo, una ingeniería viguesa que forma parte de la red de integradores de Universal Robots. Su director, Fernando Cao, nos da las claves para incrementar la amortización de un robot colaborativo y nos presenta las oportunidades de automatización que existen en la industria conservera.
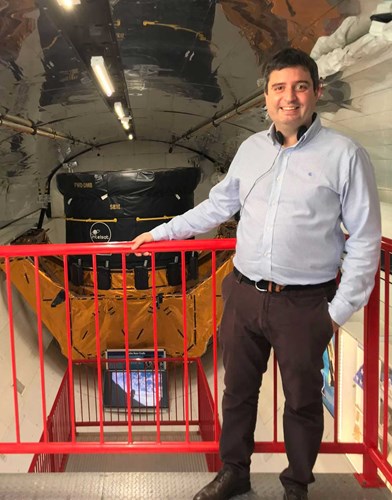
- ¿Quién es Emenasa Industria?
- Somos la división industrial del Grupo Emenasa, que empezó hace 60 años en el sector naval. Agrupamos toda la actividad terrestre del grupo. Trabajamos en sectores como automoción, alimentación, madera... Coordinamos con el resto del grupo las distintas actividades: neumática, hidráulica, mecánica, etc.
- ¿Estáis muy enfocados en el ámbito gallego, o tenéis un enfoque global?
- Aunque todas las empresas del Grupo Emenasa se centran en Galicia, hace poco fundamos Emenasa Lusitania en Viana do Castelo (Portugal). Puesto que muchos de los clientes con los que trabajamos son multinacionales, tenemos que prestar servicio allí donde estén implantados. En Galicia fabricamos las instalaciones, pero podemos hacer la puesta en marcha en cualquier parte del mundo.
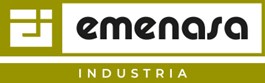
- Formáis parte del programa de integradores certificados de Universal Robots. ¿Qué significa esto para vosotros?
- El mundo colaborativo y la Industria 4.0 son una parte muy importante de nuestra línea de negocio. Dentro de ese campo, Universal Robots es una marca muy reputada. Llevamos muchos años colaborando con ellos y acumulamos un conocimiento muy interesante que el cliente valora.
- ¿Por qué apostasteis por la robótica colaborativa?
- Nuestro fuerte es la ingeniería, por lo que tenemos que estar atentos a las novedades del sector. Empezamos con la integración de PLCs hace veinticinco años y el desarrollo de la industria nos fue llevando hacia la robótica colaborativa.
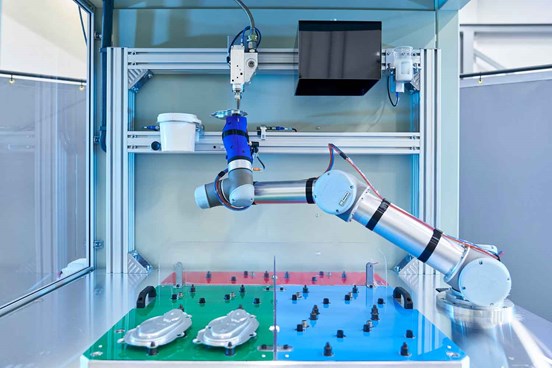
- ¿Consideras que hay una demanda creciente de este tipo de soluciones?
- Sí, es una solución muy interesante para ciertas aplicaciones. Una vez superada la fase en la que la gente quería poner un cobot en su vida porque daba fama o hacía ilusión, ahora hablamos ya de aplicaciones con retornos importantes y en tiempos cortos. Para ciertas industrias y aplicaciones, esta tecnología encaja mejor que un robot convencional. Es una instalación robusta, aunque pueda trabajar al lado de la gente.
- ¿En qué tipo de aplicaciones sería recomendable la introducción de los robots colaborativos?
- Encajan muy bien en operaciones de ayuda al trabajador que presenten una ergonomía complicada, en trabajos donde haya muy poco espacio y en tareas de control de inspección. Si no puedes tener una celda cerrada por falta de espacio o necesitas instalaciones móviles, los cobots funcionan muchísimo mejor que la robótica convencional.
- Trabajáis para numerosos sectores, pero uno de los más arraigados en la economía gallega es la industria conservera, que conocéis en profundidad. ¿Cuáles son los principales desafíos a los que se enfrenta?
- La industria conservera tiene la necesidad de una automatización intensa, pero su materia prima es producto vivo y, como tal, tiene poca repetibilidad entre sí. Para entendernos, los atunes no son tornillos. Eso ha limitado la robotización colaborativa, que se sigue manteniendo muy enfocada en el final de línea, con pequeñas cadencias e instalaciones flexibles y móviles. Cada vez hay más productos gourmet en los que el resultado debe ser precioso, y un día puedes hacer mejillones y otro día berberechos, por lo que puedes necesitar mover la instalación de una línea a otra. En cambio, para la cadena principal de fabricación de atún, que va a mil latas por minuto, el uso de cobots es complicado debido a las altas cadencias con las que se trabaja. Además, en las primeras fases del proceso de producción el entorno es muy agresivo.
- ¿Agresivo?
- Hay humedad, sal, productos desinfectantes al final de cada jornada... En estos entornos hay que proteger a los robots.
"Si no puedes tener una celda cerrada por falta de espacio o necesitas instalaciones móviles, los cobots funcionan muchísimo mejor que la robótica convencional".
- Parece disruptivo el proyecto Spectuna, que combina robótica y visión hiperspectral en la industria de la conserva. ¿Cuál es vuestro papel en él?
- Participamos en la fase de bin picking, cogiendo los atunes mediante visión 3D y, mediante una cámara hiperespectral, los caracterizamos y clasificamos en función de su composición química: de si tiene poca a mucha sal, grasa... Eso permite hacer procesados diferentes.
- ¿Proyectos como este pueden significar que en un futuro próximo la automatización colaborativa gane relevancia en todas las fases del proceso en la industria conservera?
- Sin duda. La caracterización será muy potente, porque el consumidor quiere poder elegir atún bajo en sal u otros productos muy específicos. Por tanto, tendremos que ser capaces de clasificar de manera rápida y en línea los artículos. Aún no podemos llegar a una cadencia de 1.200 latas por minuto, pero hay avances interesantes, como la posibilidad de hacer la caracterización en paralelo a la línea, o preparar los lotes lo mejor posible previamente para que los robots se ocupen de la caracterización por grupos.
Sin embargo, en tareas como la limpieza del pescado aún hay mucho camino por recorrer en cuanto a robotización, ya que hay una variabilidad grande en función del producto y la especie.
- ¿La caracterización a través de la robótica puede hacer crecer el abanico de artículos de conserva que el consumidor tiene a su disposición?
- La visión hiperespectral en tiempo real tiene dos ventajas muy grandes: evita la parte analítica de laboratorio a la hora de asegurar la calidad del producto y te ayuda a diferenciarte, por ejemplo, eligiendo los bonitos con más grasa o los más bajos en sal. Estas especificidades son muy importantes para distinguirse respecto a las marcas blancas.
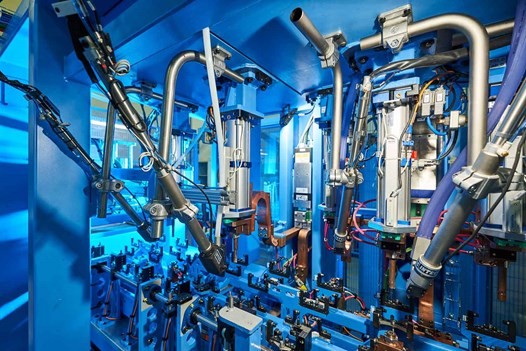
- ¿Qué otros proyectos en los que estéis trabajando este año querrías subrayar?
- Estamos haciendo bastantes proyectos de belt picking, es decir, de coger en cinta. También estamos muy enfocados en hacer instalaciones súper flexibles. El tiempo de vida de los productos cada vez es menor, mientras que la variabilidad y las exigencias de marketing son mayores. Si un cliente instala hoy un robot, mañana tiene que poder utilizarlo para otra cosa en caso de una nueva necesidad. Eso lo conseguimos con alimentadores flexibles, sistemas de visión para identificar distintas referencias y formas, garras flexibles...
"Si un cliente instala hoy un robot, mañana tiene que poder utilizarlo para otra cosa en caso de una nueva necesidad".
- Hablemos sobre el proyecto de dispensado automático de mástico para la industria del automóvil. La gran dificultad fue que había referencias con pequeños lotes y que había que aplicar mástico en piezas muy pequeñas. ¿Cómo afrontasteis el reto?
- Dio bastante trabajo. Mantuvimos una colaboración muy interesante con Universal Robots probando distintas alternativas. La aplicación de mástico y cola siempre es un punto sensible porque va directamente a producto final y no hay margen de maniobra. Por eso hay que desarrollar aplicaciones muy robustas.
La aplicación que elaboramos lleva un control unitario mediante visión e incluso permite una validación extra por parte del operario, para ofrecer las máximas garantías.
El proyecto funcionó muy bien y lo aplicamos en varias instalaciones similares. Resolvimos una aplicación que era problemática a nivel ergonómico si se hacía manualmente, porque había que manejar la pistola con muchos movimientos repetitivos y pesados.
- Enganches rápidos para cambiar de efector final, plataformas móviles... Parece que la clave de la solución fue la versatilidad, es decir, que era poco rígida. ¿Por qué consideras que es un factor importante?
- Desde el inicio sabíamos que esta instalación no sería dedicada, sino que daría servicio a diferentes piezas que se fabrican en zonas diferentes de la planta, por lo que tenía que poder moverse. Lo que el cliente necesitaba era que la solución se pudiera amortizar en el mayor número de turnos posible. Por eso lleva utillajes intercambiables en función de la referencia que se está trabajando. Solo tienes que elegir un nuevo mosaico para operar en otras piezas.
- Otra clave fue la funcionalidad TCP remoto. ¿De qué se trata?
- Fue un punto complicado, porque al trabajar con radios pequeños, la velocidad de dispensado de cola tenía que ser rápido y constante para que no se amontonara, pero nos teníamos que ir adaptando a las curvaturas cerradas. Lo conseguimos variando el objeto del TCP, que constituye el punto en el que se encuentra la pieza.
- ¿Recuerdas alguna anécdota de esa integración?
- Este cobot fue el primero que se introdujo en el grupo para quien desarrollamos el proyecto. A la planta le costó que la dirección aprobara la integración, así que hubo que recorrer un camino previo de estudio, de preparación y de que el cliente se creyera que podía lograrlo. Fue muy bonito.
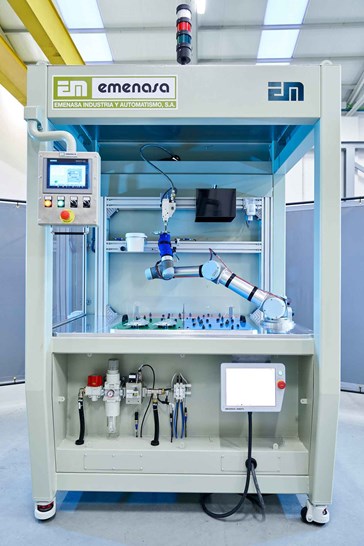
- Ingenierías como la vuestra acercan las nuevas tecnologías al territorio más allá de las grandes ciudades. ¿Qué papel puede tener la automatización a la hora de revertir la deslocalización y la despoblación en España?
- La cuestión es que no puedes incorporar tecnología puntera sin tener conocimiento sobre ella. Tu plantilla no tiene que saber desarrollar una instalación robótica, pero sí entenderla, manejarla y mantenerla. Ese es el gran reto al que se enfrenta la España vaciada: tiene que ser capaz de atraer a empleados especializados que quieran trabajar allí, algo que cada vez está ocurriendo más. Por suerte, está creciendo el número de gente formada en robótica. También es cierto que estamos reduciendo el problema y atendiendo de forma más constante a los clientes gracias al apoyo remoto para resolver incidencias.
- ¿Hacia dónde va Emenasa Industria?
-Tenemos un equipo de ingeniería muy potente en el que hemos invertido mucho a nivel de formación y tenemos que mantenerlo independientemente de la estacionalidad de nuestros clientes, por eso tenemos que diversificarnos y entrar en nuevos sectores. Por otro lado, queremos aumentar nuestra presencia en Portugal. Y, aunque somos sastres que trabajamos a medida, el sueño de cualquier ingeniería es desarrollar máquinas estándar que podamos replicar.
La contraportada
8 preguntas "out of the box"