Entrevista a Enrique Vacas, director general de Nutai
Adaptar el funcionamiento de las compañías multinacionales a la capacidad de las pymes. Ese es el secreto que ha llevado a la empresa valenciana Nutai a posicionarse como una de las ingenierías más innovadoras de España. Esta estrategia se plasma en aspectos como un organigrama que se organiza en base a departamentos especializados en tecnologías concretas, o la apuesta por una I+D que tiene que ser rentable tanto por los productos que desarrolla como por sus ingresos directos y las ayudas que recibe.
Nos interesa conocer con más profundidad a esta compañía, integrador certificado de Universal Robots, de la mano de su director general, Enrique Vacas.
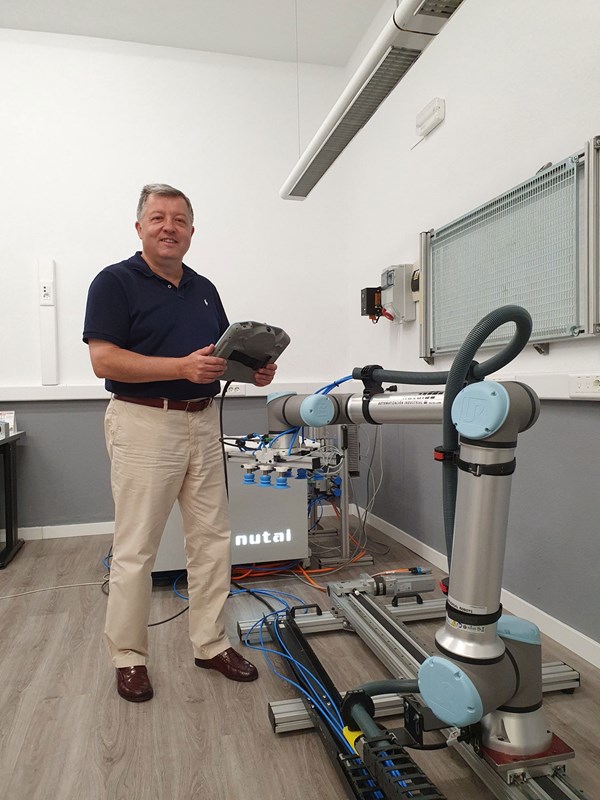
- ¿Quién es Nutai?
- Nutai es una ingeniería de proyectos e instalaciones llave en mano que fundamos mi socio Fernando Torrijos y yo en 1995 y que ahora cuenta con 45 trabajadores. Este noviembre cumpliremos 26 años. Durante este tiempo, nos hemos centrado en la introducción de nuevas tecnologías en el tejido industrial.
El sector en el que más trabajamos desde el principio, y en el que nos focalizamos hace doce años, es el de la automoción. La ventaja es que es una industria pionera en la utilización de nuevas tecnologías, tanto en cuanto a sistemas y equipos como a nivel de organización industrial y mejoras en los sistemas de producción. Eso hace que siempre tengas que estar en la cresta de la ola. Muestra de ello es la utilización de la robótica colaborativa. De ahí que en los últimos cinco años nos hayamos especializado en lo que se denomina Industria 4.0.
“Nuestro rasgo distintivo es que siempre hemos estado en contacto con nuevas tecnologías y hemos tenido la capacidad de introducirlas en proyectos reales.”
- ¿Recuerdas qué proyecto concreto os llevó a apostar por la robótica colaborativa?
- Fue en el segundo semestre de 2015 en Ford España. La gerencia de la planta de motores de Valencia y su equipo técnico tenía interés en utilizar robots colaborativos. Nosotros ya habíamos participado con Ford en la introducción de nuevos sistemas y equipos. Así pues, estuvimos trabajando durante seis meses para hacer un estudio y estandarizar la introducción de cobots en la planta.
En abril de 2016, implantamos el primer cobot en la factoría de Ford en Valencia. Era un cobot UR para un aplicativo que consistía en colocar y apretar cuatro bujías en la línea de montaje de motores.
- Esta forma de trabajar tan cerca de lo que el cliente necesita os debe mantener atentos a las tecnologías que despuntan y formándoos constantemente.
- Aunque somos una empresa pequeña cuyo número máximo de empleados fue de 65 personas, tenemos los mismos departamentos que una multinacional. Tenemos departamentos transversales, como pueden ser compras, recursos humanos, logística, comercial y gerencia. Pero también contamos con departamentos verticales a nivel tecnológico, como ingeniería eléctrica, ingeniería mecánica, software, visión artificial y dos áreas muy importantes: gestión de proyectos e I+D.
El departamento de I+D tiene dos objetivos: en primer lugar, el desarrollo de producto propio, como el que lanzamos recientemente para controlar ejes lineales de Festo para cobots de Universal Robots, incluido dentro de la plataforma UR+; y en segundo lugar, la industrialización de nuevas tecnologías. Por tanto, es el encargado de coordinar al resto de departamentos para estandarizar la aplicación industrial de nuevas tecnologías.
Fue este departamento quien arrancó la introducción de la robótica colaborativa en Ford España.
- Formáis parte del programa de integradores certificados de Universal Robots. ¿Qué significa esto para vosotros?
- Para mí la aparición de Universal Robots en el cosmos de la tecnología ha sido disruptiva, tanto por su producto como por su modelo. El canal de distribución de productos de UR se divide en distribuidores e integradores. Como ingeniería, encajamos perfectamente en la segunda área. Pero la clave es que entre distribuidores e integradores no nos hacemos competencia, sino que vamos de la mano.
“El ecosistema de desarrolladores de UR está muy bien inspirado en las tecnológicas, y ha hecho que empresas como la nuestra, con un nivel tecnológico medio alto, participen de un entorno en el que nos sentimos muy a gusto.”
Es un business-to-business-to-client real.
Desde mi punto de vista, ahora mismo no hay ninguna otra marca de tecnología industrial que lo haga de la misma manera.
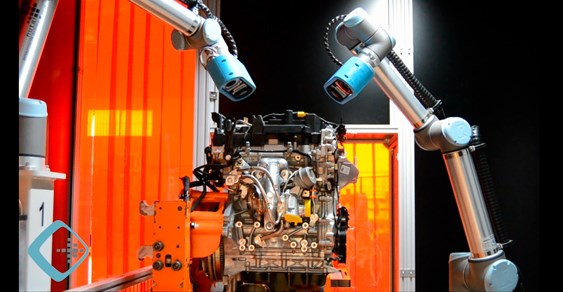
- Fuisteis reconocidos como pyme innovadora por el Gobierno de España. Teniendo en cuenta que en nuestro país la inversión en I+D sigue por debajo de la media europea, ¿qué recomendaríais a las empresas que quieran aumentar su capacidad innovadora?
- No hemos descubierto nada, hemos adaptado a nuestras capacidades lo que hacen los grandes. Ellos destinan un porcentaje de su facturación o sus beneficios a I+D y aprovechan todas las herramientas que ofrece ya no la Comunidad Valenciana o España, sino la Unión Europea.
“Es decir que, dentro del balance de las grandes compañías, la gestión y consecución de ayudas para I+D es un activo muy importante. ”
Las pymes tenemos que hacer lo mismo: conseguir que el departamento de I+D sea rentable, tanto por el producto o servicio que desarrolla como por los ingresos tanto directos como en forma de ayudas fiscales que obtiene.
- Estáis implicados en el proyecto europeo Acroba de robótica cognitiva. ¿Cuál es vuestro papel?
- Es nuestro primer proyecto europeo. Hace unos trece años habíamos arrancado con proyectos en el ámbito de la Comunidad Valenciana y, más adelante, en iniciativas nacionales con el Centro para el Desarrollo Tecnológico Industrial (CDTI) y clústers de Automoción y Energía.
Acroba es un proyecto de robótica cognitiva, un concepto que ahora mismo no existe pero que precisa de un entorno demostrativo real. En el consorcio de diecisiete empresas, centros tecnológicos y universidades de este proyecto se encuentran tecnólogos de alto nivel que son expertos en tendencias de la robótica, actores que tienen un punto de vista mucho más práctico pero no están avezados en la industria, posibles usuarios finales e integradores como nosotros. Nuestra función es entender tanto a los gurús como las necesidades del cliente final y la realidad de la industria, a veces basta y burda, y ponerlos en conexión.
- Uno de vuestros proyectos más recientes tuvo lugar en una planta británica de un gran fabricante de automóviles. Consistió en un sistema de inspección final de motores capaz de analizar 50 parámetros en menos de un minuto. ¿Cuál crees que fue la clave del éxito?
- Ford ya conocía nuestra experiencia en la implantación de robótica colaborativa, pero el gran reto del proyecto estaba en la parte de visión artificial. La clave fue que les aportamos seguridad en las dos vertientes. Además, el cliente confío en nosotros porque éramos competitivos a nivel económico y porque teníamos recursos propios, es decir, no teníamos que subcontratar tecnología y nuestros especialistas podían hacer un llave en mano. En el proyecto participaron todas nuestras áreas de ingeniería: eléctrica, mecánica, visión artificial y software. Además, el departamento de I+D planteo dos innovaciones: la lente líquida y el uso de luz ultravioleta.
- ¿Qué aportaban estas dos innovaciones?
- En esta instalación, los cobots hubieran tenido que posicionarse en varios lugares alrededor del motor, pero teníamos que hacer un número de inspecciones muy alto en un tiempo de ciclo corto. La lente líquida es un sistema de óptica que permite variar el foco desde una misma posición física. De esta manera, puedes hacer una foto concreta de una parte pequeña del motor y, sin moverte, tomar la imagen de una zona alejada. Por tanto, ahorras tiempo porque el cobot no tiene que estar reposicionándose.
En cuanto a la luz ultravioleta, en visión artificial tan importante es la elección de las cámaras como de las iluminaciones y filtros. La luz ultravioleta nos permite identificar fugas, en este caso de aceite lubricante y de otros fluidos en el motor. Sin este tipo de iluminación y filtro, la cámara no las detectaría.
- ¿Qué ventajas crees que aporta combinar la robótica colaborativa con la tecnología de visión artificial?
- La visión artificial es un aplicativo que el cobot puede mover de manera muy razonable dentro de su capacidad de carga de entre 3 y 16 kilos. El cobot permite utilizar esta tecnología en un entorno de seguridad y a unos tiempos de ciclo adecuados.
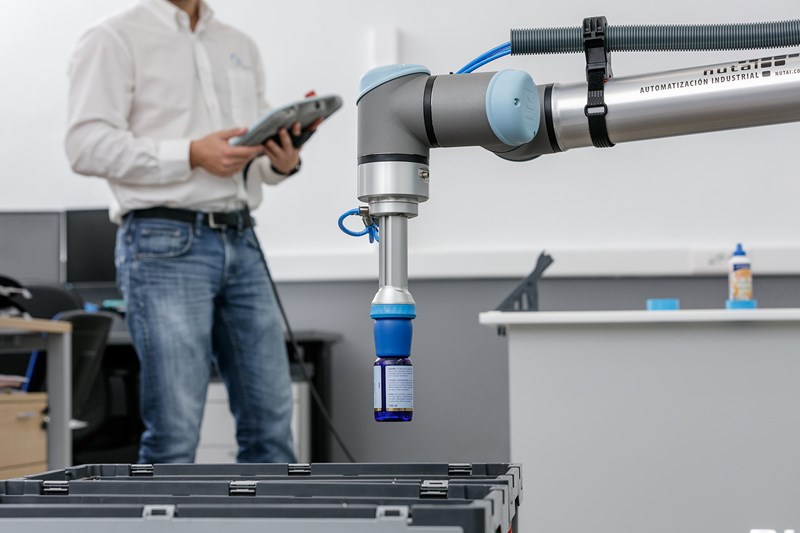
- Otro aspecto clave del proyecto es la trazabilidad de los motores que permite la robótica colaborativa. ¿Es un ejemplo de las posibilidades de la Industria 4.0?
- En nuestro proyecto con Ford encontramos tres pilares de la Industria 4.0: la robótica colaborativa, la visión artificial y la trazabilidad industrial. En todo momento del proceso, el sistema identifica el motor que está inspeccionando y relaciona el número de identificación del motor con el chequeo que hace al equipo. A partir de ese momento, se genera una especie de “cartilla de vacunación” del motor. Durante toda su vida útil, sabremos qué se inspeccionó, cuándo, cómo y con qué resultados.
- ¿Recuerdas alguna anécdota durante el proceso de implementación?
- Con los ingleses siempre hay historias, porque lo hacen todo al revés (ríe), empezando por conducir, pero trabajamos muy bien con el equipo inglés. Hubo una anécdota, y es que en España el reglamento indica que las interconexiones de un modelo determinado a una tensión concreta necesitan un cableado de colores muy específicos: marrón, azul y negro. En cambio, la norma inglesa, que teóricamente es global pero solo se aplica en Reino Unido, indica que el cableado tiene que ser bicolor o tricolor con otros colores. Y no había manera de encontrarlo, ni siquiera en Reino Unido. Nos costó un poquito más de lo normal (ríe).
A partir de ahí, no hubo problemas: hicimos lo que teníamos que hacer, de la manera que teníamos que hacerlo y en el plazo en el que teníamos que hacerlo.
- Estamos hablando de un proyecto internacional y muy ambicioso. ¿Crees que las ingenierías españolas están en una buena posición para atraer y completar con éxito este tipo de proyectos?
- Las ingenieras españolas estamos muy bien posicionadas a nivel tecnológico. Podemos competir con cualquier otra ingeniería del mundo. No tenemos limitaciones en ese aspecto. Nuestro handicap es la falta de centros de decisión de grandes multinacionales en España. Si una empresa decide en Alemania, hará un porcentaje muy alto del trabajo con empresas alemanas.
- ¿Cómo la experiencia con grandes clientes puede beneficiar a las pymes que acuden a vosotros?
- Muchísimo, porque los grandes clientes nos dan una visión y una forma de trabajar que de otra manera sería imposible. Por ejemplo, trabajar con Ford, SEAT, Volkswagen, Renault, Nissan, Gestam o Antolin nos da acceso a la alta tecnología y, algo muy importante, a la aplicación de esas tecnologías en entornos reales. Trasladar nuestra experiencia a pymes y no tan pymes de otros sectores nos da una ventaja competitiva importante.
- ¿Podrías compartir con nosotros alguno de los proyectos más ilusionantes de Nutai en 2021?
- Por una parte, tenemos el proyecto Acroba de robótica cognitiva, que puede marcar una forma de trabajar en los próximos cinco o diez años en el ámbito de la robótica.
A nivel estratégico, estamos focalizándonos en proyectos de I+D relacionados con la automatización del reciclaje de baterías de vehículo eléctrico.
Por otra parte, en breve tendremos el lanzamiento de un motor nuevo en Valencia, un 2.0 que se lanzará a partir del segundo semestre de este año. También se ha anunciado que viene un motor gasolina de 2.5 como soporte a los motores híbridos enchufables que monta Ford, y esperamos poder entrar en el proyecto.
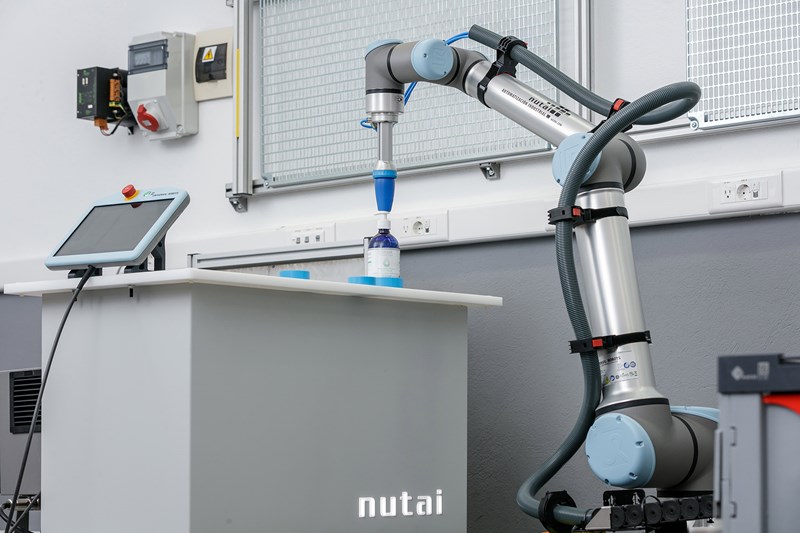
La contraportada
8 preguntas "out of the box"