Revlon, la icónica marca de productos de belleza y cuidado personal, ha catapultado la productividad en su planta en el Pla de Santa María, Tarragona. Esta instalación de 40,000 m² desempeña un papel clave en la fabricación de productos como colonias, desodorantes y tarros de skincare de alta calidad, destinados a mercados internacionales. La planta cuenta con 20,000 horas anuales de envasado, 15 reactores y un almacén automático.
En respuesta a las crecientes demandas del mercado y con el objetivo de mejorar la ergonomía en el trabajo, Revlon ha apostado por la automatización avanzada en su línea de producción de skincare. Gracias a un sistema de encajado y paletizado automático desarrollado por WeCobots, que incluye tres robots colaborativos de Universal Robots, la empresa ha transformado sus operaciones del final de línea. Un avance que ha permitido reducir tiempos de ciclo, aumentar la capacidad de respuesta y liberar a los operarios de tareas repetitivas.
El reto:
Revlon necesitaba una solución que ofreciera flexibilidad y eficiencia para manejar múltiples productos, simplificando los cambios de formato sin comprometer la calidad ni aumentar los costes. Además, era fundamental optimizar el espacio disponible en la planta, garantizando al mismo tiempo la seguridad de los operarios.
El trabajo manual, que implicaba manipular tarros de hasta medio kilo, había ocasionado problemas ergonómicos en el personal, como túnel carpiano y molestias físicas derivadas de esfuerzos repetitivos. Además, mantener el ritmo de la línea resultaba complicado para los operarios, lo que limitaba la eficiencia de la producción.
El objetivo era contar con un sistema que permitiera a los operarios trabajar de manera segura, reducir los tiempos de cambio de configuración y eliminar la dependencia de herramientas costosas y complejas.
La solución:
En enero de 2024, Universal Robots integró un sistema de automatización compuesto por tres robots colaborativos UR10 que se encargan actualmente de las operaciones críticas del final de línea, incluyendo:
- Conformado de cajas
- Encajado y precintado
- Etiquetado
- Paletizado
Todo el proceso se gestiona desde un panel de control centralizado, diseñado para ser intuitivo y fácil de manejar, incluso para operarios con formación básica. Esta plataforma permite supervisar, ajustar parámetros y resolver incidencias de manera eficiente, lo que agiliza las operaciones y simplifica los cambios de formato. Cada estación se gestiona desde un escritorio central, donde los operarios pueden realizar movimientos manuales, gestionar alarmas y rearmar el sistema en caso de colisiones de seguridad, sin necesidad de manipular los paneles.
Los cobots destacan por su flexibilidad y facilidad de uso, lo que minimiza los costos asociados a nuevos formatos y elimina la necesidad de técnicos especializados. Además, su diseño compacto, que ocupa menos de 25 m², y su capacidad para adaptarse a diversos productos sin requerir grandes inversiones en utillajes, los convierten en una solución altamente eficiente y versátil.
Durante la implementación, surgieron desafíos iniciales, como roturas en las cajas y fallos en la precintadora. Sin embargo, estos problemas fueron solucionados mediante ajustes y mejoras en el sistema, demostrando la capacidad de adaptación tanto del equipo técnico como de los robots colaborativos.
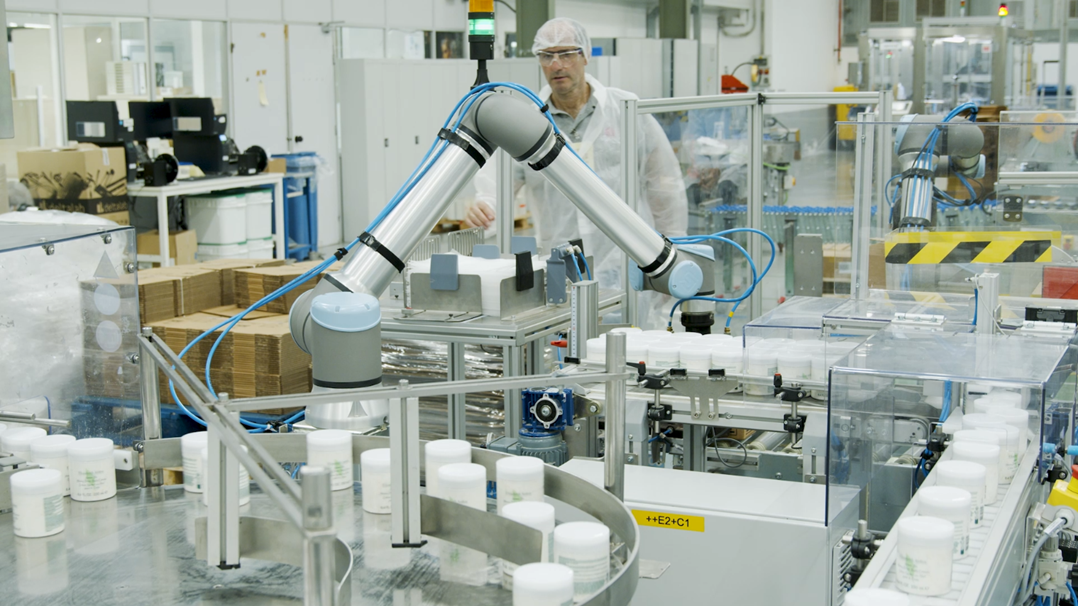
Los resultados:
- Flexibilidad y adaptación: Ahora la línea puede manejar diversos productos sin necesidad de grandes inversiones adicionales en piezas o utillajes. Los cambios de formato ahora son más rápidos y económicos, gracias a la flexibilidad del sistema.
- Compatación y seguridad: La estación ocupa menos de 25m², es óptima para el uso del espacio en la planta y ofrece un entorno seguro.
- Eficiencia operativa: Desde su implementación, el sistema ha demostrado resultados inmediatos y ha gestionado casi 2,5 millones de tarros, realizando 205,000 ciclos en solo ocho meses.
- Garantía de calidad: La célula incluye controles específicos para asegurar la precisión en el etiquetado y la consistencia en todas las etapas del proceso.
IMPACTO EN EL NEGOCIO
La automatización ha permitido a Revlon mantenerse ágil frente a las demandas del mercado y a los lanzamientos de nuevos productos, fortaleciendo su competitividad en el ámbito global. La flexibilidad, seguridad y simplicidad del sistema han sentado las bases para replicar esta tecnología en otras líneas de producción, posicionando a la compañía como un referente en la adopción de innovaciones tecnológicas.
La incorporación de los cobots ha sido recibida de manera positiva por los operarios, quienes destacan la facilidad de uso del sistema y las mejoras significativas en sus condiciones laborales. Esta automatización también ha enfrentado con éxito el desafío de encontrar personal dispuesto a realizar tareas manuales, un problema cada vez más común en el sector.
De cara al porvenir, Revlon destaca la importancia de contar con sistemas flexibles capaces de adaptarse a nuevos productos y a los avances en robótica e inteligencia artificial. A pesar de los retos que supone justificar ciertas inversiones en digitalización, la empresa confía en que estas iniciativas seguirán siendo clave para su éxito.
"La implementación de los robots colaborativos de Universal Robots nos ha permitido, además de optimizar los tiempos de producción, mejorar las condiciones de trabajo de nuestros operarios. Ahora podemos adaptarnos rápidamente a nuevas demandas sin grandes inversiones adicionales. Nuestra idea es, con el tiempo, transversalizar esta misma célula en otras líneas" señala Romuald Reñé, Project Engineer de Revlon