Las empresas manufactureras han encontrado en los robots para trabajos peligrosos un aliado fiable para diseñar plantas de producción adecuadas para la prevención de riesgos. El hito de los “cero accidentes laborales” no parece tan lejano si es un brazo robótico el que se encarga de coger, levantar, dejar, soldar, atornillar, pulir y otros tantos verbos que nos trasladan al trabajo físico, desgastante y, a veces, peligroso.
La prevención de riesgos laborales se halla en la cima de las preocupaciones de una empresa. En primer lugar, para garantizar la seguridad e integridad de los trabajadores y un entorno de trabajo saludable y agradable. Pero también hay una razón económica y operativa: cada accidente laboral supone una media de 11,4 días de baja, según cálculos de Mutua Asepeyo, con los perjuicios que ello conlleva para la organización de la compañía.
Aún nos resultan cercanos los picos más afilados de la pandemia de COVID-19. Y en esos días angustiosos muchas empresas comprobaron lo que significa no poder disponer de la plantilla al completo por problemas de salud.
En este sentido, los robots para trabajos peligrosos pueden evitar una “epidemia” de accidentes laborales en tu planta industrial.
Incidencia de los accidentes laborales en España en 2021
Es fácil reconocer el impacto de los robots para trabajos peligrosos en la reducción de la siniestralidad laboral, si nos atenemos a las cifras. De los 497.735 accidentes laborales con baja que se produjeron en el centro de trabajo en 2021, según datos del Ministerio de Trabajo y Economía Social:
- El 31% estuvieron causados por un sobreesfuerzo físico sobre el sistema musculoesquelético.
- El 26%, por golpes contra un objeto inmóvil.
- El 15%, por choques o golpes contra objetos en movimiento.
- El 10%, por el contacto con objetos cortantes o punzantes.
En total, estos factores generan 8 de cada 10 siniestros. Son cuatro riesgos con los que las fábricas tienen que lidiar casi a diario. Cuatro riesgos que un robot colaborativo puede reducir drásticamente gracias a su capacidad para efectuar movimientos repetitivos y cargar hasta 20 kg. Asume, por tanto, las labores físicas y extenuantes, y deja la supervisión, la resolución de problemas y la coordinación a los empleados.
Entornos colaborativos para reducir la siniestralidad laboral
La Ley de Prevención de Riesgos Laborales establece las obligaciones de las empresas para prevenir la siniestralidad laboral, ordenando “un conjunto coherente y globalizador de medidas de acción preventivas adecuadas a la naturaleza de los riesgos detectados y el control de la efectividad de dichas medidas”.
Y, entrando más en detalle, la normativa obliga a “adaptar el trabajo a la persona, en particular en lo que respecta a la concepción de los puestos de trabajo, así como a la elección de los equipos y los métodos de trabajo y de producción, con miras, en particular, a atenuar el trabajo monótono y repetitivo y a reducir los efectos del mismo en la salud”.
Volvamos atrás: “Atenuar el trabajo monótono y repetitivo”. Este punto pone de manifiesto la importancia de la automatización de los procesos para reducir el riesgo de accidentes laborales.
¿Cuál es el problema? Que tradicionalmente los robots para trabajos peligrosos eran de gran envergadura y pesados. Aunque pueda parecer paradójico, necesitaban una infraestructura de seguridad a su alrededor para funcionar sin peligro. Por tanto, eran una quimera para plantas productivas pequeñas y con presupuestos reducidos.
Todo esto cambió con la llegada de los robots colaborativos: son ligeros, están diseñados con formas redondeadas y cuentan con sensores inteligentes que les hacen detenerse en caso de choque, obstrucción o entrada de un operario en su espacio de trabajo. Por tanto, los cobots pueden compartir espacio y dinámicas de trabajo con los empleados. Y pueden ubicarse en áreas pequeñas. Entonces, ¿estamos ante los auténticos robots para trabajos peligrosos?
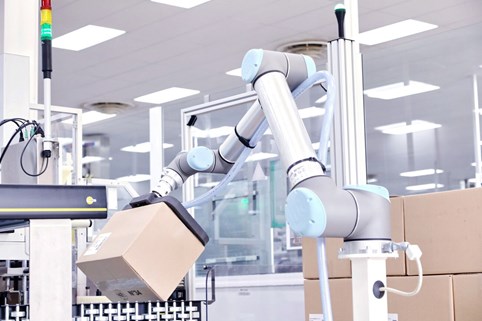
¿Los cobots son robots para trabajos peligrosos?
La respuesta concisa es que sí. Los cobots tienen todas las condiciones para que una empresa industrial garantice un nivel de seguridad óptimo. Pero como siempre que se habla de riesgos laborales, toda prevención es poca.
Los cobots se configuran para desempeñar determinadas aplicaciones. No solo entra en juego el brazo robótico, sino también el software de programación, la sensórica, la herramienta de final de brazo, los equipos con los que interactúa, el entorno y los flujos de trabajo…
“La interacción entre la persona y el robot puede ser totalmente segura, pero para ello debemos implementar aplicaciones en las que se tomen todas las medidas preventivas posibles y aportar seguridad a la aplicación”, explicó Raúl Burgos, Sales & Account Manager de Inexpect Iberia, durante el congreso Collaborate Pack celebrado en Barcelona.
Por esa razón es imprescindible realizar una prueba de evaluación de riesgos antes de poner en marcha una instalación. “Cualquier proceso de automatización colaborativa cuenta con un minucioso proceso de seguridad que ha estado testado previamente y nos permite tener el control absoluto sobre su funcionamiento”, comentó a este respecto Pablo Fernández, CEO de Solidsafe.
Si quieres informarte sobre la posibilidad de instalar robots para trabajos peligrosos en tu fábrica, te invitamos a ponerte en contacto con uno de nuestros expertos.