WECOBOTS, la unidad de ingeniería de robótica colaborativa del grupo WETRON, inició su andadura en el mundo de los cobots por la puerta grande: uno de sus primeros proyectos consistió, nada más y nada menos, que en automatizar la colocación de siglas en los modelos Ibiza y Arona de SEAT Martorell. Lo que ahora es un caso de éxito que ha dado la vuelta al mundo fue en sus inicios una apuesta compleja, no exenta de contratiempos y dificultades. Oscar Orcajo y Alberto Hernando lideraban el equipo de WECOBOTS que protagonizó la hazaña.
Hemos hablado con ellos de los obstáculos, soluciones y aprendizajes que muestran el poder de la creatividad y la innovación en el mundo de la robótica colaborativa.
Entrevista a Oscar Orcajo y Alberto Hernando, de WECOBOTS
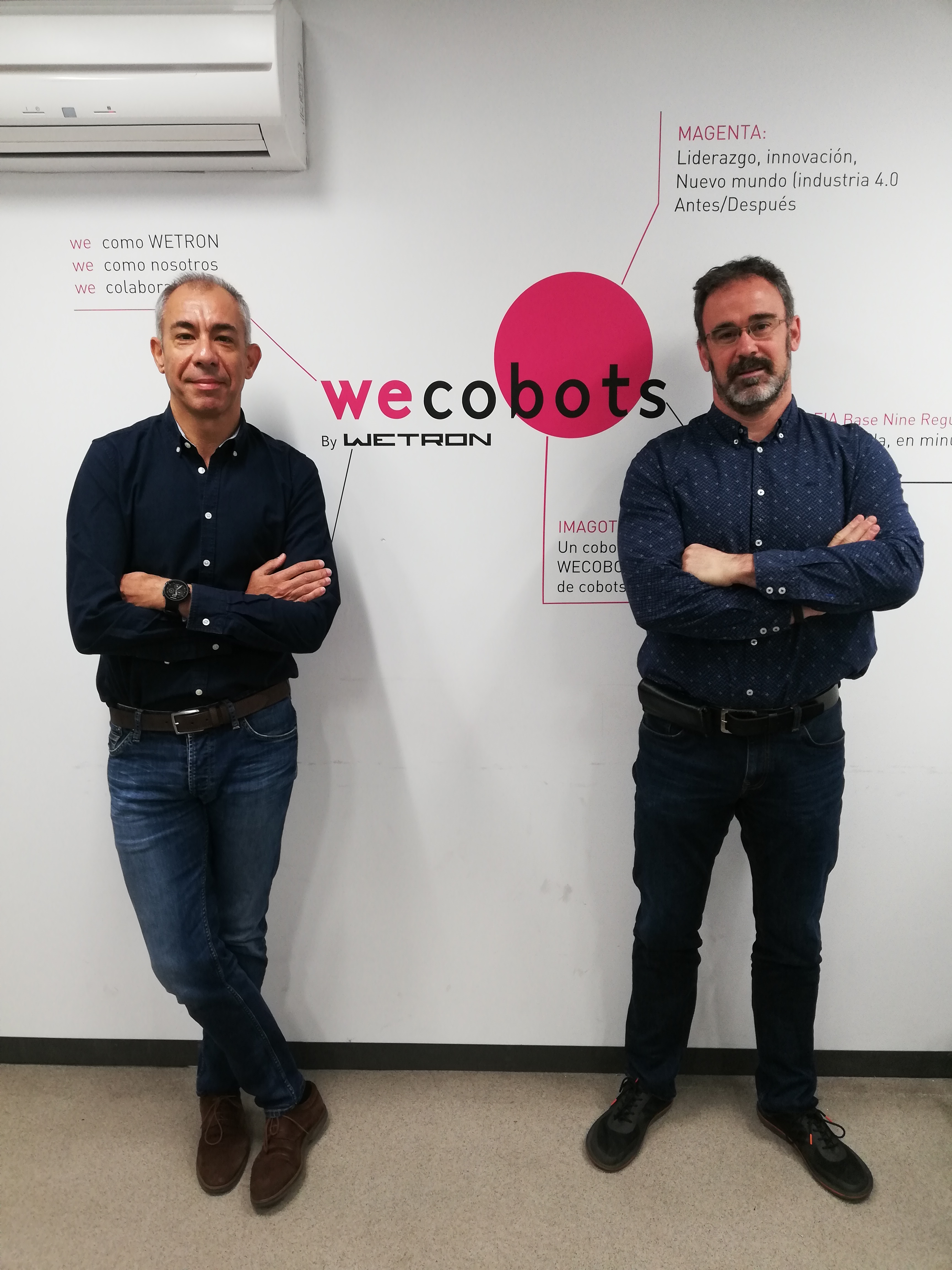
¿Qué es WECOBOTS?
- AH: WECOBOTS es nuestra unidad de ingeniería especializada en la integración de cobots. Además, somos un CSI (Certified System Integrator) de Universal Robots, y nos hemos especializado en sus robots colaborativos para el desarrollo de nuestras soluciones.
Empezamos nuestra andadura hace tres años para dar respuesta a la necesidad de soluciones de Industria 4.0 de nuestros clientes históricos en el campo de la automoción, como era el caso de SEAT. Ahora, gracias a nuestra experiencia de más de 25 años en las soluciones de automatización industrial, nos hemos posicionado rápidamente como un especialista de las soluciones con robots industriales para las operaciones de montaje, manipulación, alimentación de máquina, dosificado y cualquier otra solución con cobots.
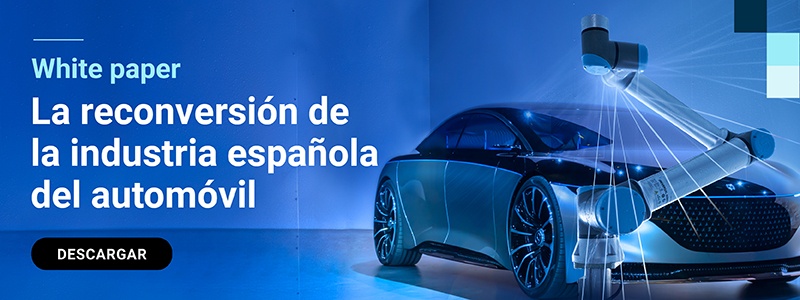
Uno de los primeros proyectos que desarrolló WECOBOTS fue la instalación de robots colaborativos nada más y nada menos que en la línea de producción de SEAT Martorell. ¿Cómo vivisteis esa oportunidad?
- OO: La oportunidad surgió cuando estábamos empezando en la robótica colaborativa. No podíamos arrancar al 100% y estábamos en un proceso de aprendizaje. Fue entonces cuando se nos presentó la posibilidad de automatizar el montaje de siglas en SEAT. Para nosotros era como apuntarnos a una maratón cuando habíamos empezado a correr, pero teníamos que decidir si cogíamos el tren o no. Dada la complicación del encargo, que rayaba lo imposible, varias empresas competidoras con más experiencia habían decidido no subirse al proyecto. Nosotros lo vimos como una oportunidad. Conocíamos a SEAT y ya habíamos desarrollado para ellos otros proyectos complicados. Además, tenemos gladiadores, más que programadores, así que decidimos embarcarnos. Eso sí, el proceso ha costado muchísimo y el equipo ha tenido que poner el alma.
¿Cuáles eran los desafíos que os planteó el cliente?
- OO: El principal desafío era hacer una instalación colaborativa en montaje dinámico. Es decir, el robot tenía que coger las siglas y montarlas en la carrocería que estaba en movimiento. Además, el tiempo de ciclo de los modelos Ibiza y Arona es rápido, de un minuto. SEAT también nos pidió una instalación colaborativa que debía operar en poco espacio, conviviendo con los operadores, que bien podían trabajar en la misma tarea que el robot o realizar labores complementarias en el mismo vehículo.
¿Qué reto supuso para vosotros un proyecto de esta envergadura y cómo lo afrontasteis?
- OO: El proyecto no arrancó desde el departamento I+D de SEAT, donde la planificación no es lo más importante, sino que lo hizo desde el departamento de procesos, como cualquier proyecto de industrialización estándar. Por lo tanto, más allá de las dificultades técnicas, para nosotros fue un gran reto adecuarnos al planning existente. Entendimos que no iba a ser fácil cumplir con todos los requisitos del proyecto, teniendo en cuenta, además, el plus de exigencia que tienen los trabajos en el sector de la automoción. Por otra parte, no podíamos fallar, porque nos jugábamos nuestra reputación, estábamos comprometidos con el éxito.
{% video_player "embed_player" overrideable=False, type='scriptV4', hide_playlist=True, viral_sharing=False, embed_button=False, autoplay=False, hidden_controls=False, loop=False, muted=False, width='1280', height='720', player_id='29320615686', style='' %}
Hablemos del proceso de aprendizaje y de ensayo que os permitió dar con la solución definitiva.
- OO: Al principio, trabajamos como en cualquier otro proyecto: planteamos una idea, preparamos la documentación mecánica y eléctrica y la fabricamos. Sin embargo, después de haberle dedicado tanto esfuerzo y recursos en forma de planos, piezas y dinero, no funcionaba; la idea no era válida. Aprendimos una lección importante: las ideas hay que plasmarlas de forma sencilla y rápida y, si es necesario, transformarlas en un prototipo sobre madera de marquetería. Fruto de esa enseñanza, ahora contamos con una impresora 3D que nos permite materializar las ideas. Equivocarnos ya no es un problema, porque probamos de manera rápida y sencilla.
¿Por qué elegisteis los robots colaborativos de Universal Robots para este proyecto?
- OO: Cuando comenzamos a trabajar en el sector, exploramos la oferta del mercado y vimos que Universal Robots era el fabricante número uno por ventas, modelos y ecosistema de proveedores. Al trabajar para el sector del automóvil, siempre apostamos por productos de primeras marcas. Universal Robots nos aporta mucho valor añadido en cuanto a documentación, formación, servicio técnico, postventa… Son aspectos calve para tirar adelante un proyecto, y hemos visto una gran diferencia en comparación con otros fabricantes.
¿Cómo fue la colaboración con Universal Robots?
- AH: Muy positiva. Podemos decir que WECOBOTS ha crecido de la mano de Universal Robots. La relación de UR con nuestros técnicos ha sido muy estrecha en aspectos como la formación y la asistencia. Además, contamos con un robot UR en nuestras instalaciones para la formación tanto interna como externa y para hacer pruebas de concepto, con las que estudiamos la viabilidad de los proyectos que llevamos a cabo con nuestros clientes. En la implementación en SEAT, Universal Robots y su canal de distribución Vicosystems colaboraron en todo momento ante las dificultades que surgieron.
¿Cómo funciona la solución de colocación de siglas automatizada que habéis desarrollado?
- OO: Las siglas son complicadas de manejar, almacenar y dispensar. Están cubiertas con dos papeles: uno que protege el adhesivo y otro que hace de plantilla para unir las letras sueltas. Nuestra solución parte de unos dispensadores por gravedad en el brazo robótico UR10 que dejan las siglas en una mesa negra. Gracias a este fondo oscuro, con una cámara de visión artificial podemos coger las siglas con precisión después de haberlas fotografiado. A continuación, el brazo robótico se acerca a un poste, que extrae el papel de protección de las siglas y hace un doblez que, al final del proceso, permitirá agarrar y extraer el segundo papel, que es el que conforma las letras.
Hay que tener en cuenta que, al trabajar en movimiento, la carrocería se mueve en tres dimensiones y no podemos saber en qué punto de la cadena de montaje se encuentra. Por eso, aprovechamos la sensibilidad del cobot, que lo hace detener en caso de golpear con un objeto. Lo que hacemos es que el robot avance ciego en su eje X con las siglas hasta que toca la carrocería, y con una cámara determinamos los ejes Y y Z. A partir de entonces, aplica una fuerza constante y durante un tiempo concreto, que hemos predefinido, para fijar las siglas en el vehículo.
Finalmente, con una pinza, el robot retira el film que hace de plantilla y lo deposita en un contenedor para reciclar.
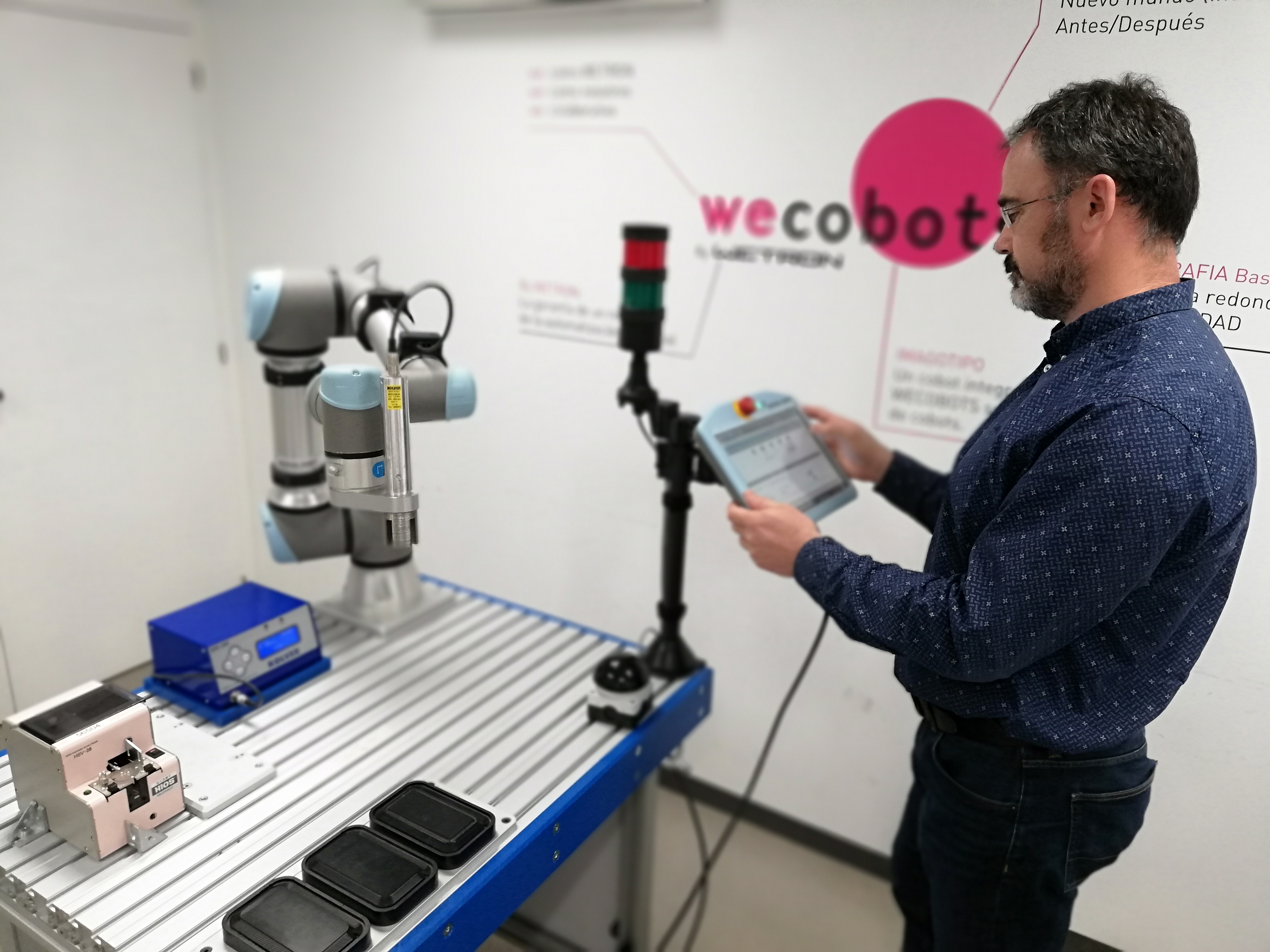
¿Recordáis alguna anécdota de los obstáculos que os encontrasteis por el camino?
- OO: En general los talleres de montaje en el automóvil son los más concurridos y donde más personal trabaja. Además, el taller 8 es el más cercano a la puerta, por lo que hay mucho tránsito de gente. Durante el proyecto muchas personas se acercaron a ver qué hacíamos. Recuerdo que un técnico de SEAT nos dijo: “¿Pero a quién se le ha ocurrido esto? Esto es imposible: las carrocerías se mueven en un skid y tenéis que pegar la sigla con una tolerancia de un milímetro, presionando y sin rayar el coche. ¿Cómo os habéis metido aquí?”. Meses después, venía con compañeros a enseñarles la instalación ya operativa. Llegó un momento en el que los programadores hacían más presentaciones que revisiones de puntos pendientes.
¿Qué ventajas está aportando la robótica colaborativa en comparación con la automatización tradicional?
- OO: Por un lado, los robots colaborativos trabajan en espacios reducidos. Normalmente, la zona de trabajo en automoción es de seis metros, en los que se encuentra el trabajador y el vehículo. En este proyecto, el espacio que se ocupa es solo de dos metros y medio.
Por otro lado, la implantación de la robótica colaborativa es más simple. Un robot tradicional puede pesar entre 200 y 300 kilos, y necesita una peana grande, grandes taladros en el suelo, vallas de protección… Su instalación exige una parada técnica larga. En cambio, los cobots pueden implantarse en un fin de semana. Por todo ello, los robots colaborativos están abriendo nuevas posibilidades, tanto en sector de la automoción como en otros sectores.
Vuestra solución integra distintas innovaciones, como el sistema de guiado por visión Cognex. ¿En qué medida veis necesaria la colaboración entre distintos fabricantes de soluciones de automatización?
- AH: WETRON lleva muchos años trabajando en un sector tan duro y estricto como el de la automoción, con exigentes normativas y planificaciones. Para cumplir tanto en planning como en resultado final desarrollando e integrando una instalación correctamente, tienes que rodearte de colaboradores punteros y 100% fiables que aporten garantías técnicas en cada una de las especialidades, como es el caso de Cognex (BCNVisión) en el campo de la visión. Nosotros conocemos las dificultades de la automatización industrial, sabemos gestionar un proyecto y nos manejamos bien con los timings y con las necesidades del cliente, pero no somos expertos en todas las tecnologías. Por eso consideramos que es tan importante la colaboración y nos rodeamos de los especialistas adecuados para cada proyecto.
SEAT ha puesto de relieve el éxito de la solución que habéis desarrollado a través de la publicación de un video en su web. ¿Qué efectos ha tenido esta buena acogida?
- AH: Tiene mucho valor en un sector donde la confidencialidad es la norma. Consideramos que SEAT reconoce así el éxito de un proyecto tecnológicamente muy complejo. La publicación ha tenido bastante repercusión en el entorno industrial. De hecho, nos ha posicionado como un integrador de robótica colaborativa que sabe desarrollar soluciones complejas y aportar un alto valor tecnológico.
Además, dentro del consorcio del Grupo Volkswagen, ha habido otras factorías que se han interesado en proyectos parecidos. También nos han consultado otros fabricantes que quieren automatizar la colocación de siglas o emblemas y realizar otras operaciones de montaje.
Por otra parte, como al mismo tiempo hemos conseguido éxitos importantes en la alimentación de máquina, el atornillado, el presionado, e incluso en el dosificado, tenemos la confianza de saber desarrollar soluciones complejas con cobots de una forma general.
¿Es posible trasladar el bagaje adquirido en la industria automotriz a otros sectores con empresas más pequeñas?
- AH: Por supuesto, ese es nuestro objetivo. Conseguir un reto como el de las siglas de SEAT nos sirve para dar confianza a empresas de primer orden. Pero, en realidad, el proyecto de WECOBOTS es más amplio: estamos haciendo llegar la automatización colaborativa a medianas y pequeñas empresas a partir del desarrollo de lo que hemos llamado “soluciones universales”. Es decir, soluciones concretas, no necesariamente complejas, que se pueden generalizar a sectores muy diversos.
Por ejemplo, nuestras soluciones móviles de alimentación de máquina con cobots UR se adaptan a varias necesidades en una misma fábrica. Ya están funcionando con éxito en las instalaciones de un fabricante de frenos, pero pueden, fácil y rápidamente, adaptarse a un gran número de operaciones en diferentes industrias.
Lo que es interesante es que, una vez que nuestros clientes, pequeños o grandes, abren la puerta a los cobots, entienden mejor sus ventajas y nos solicitan para nuevos proyectos. Para nosotros, esa es la mejor prueba del éxito de nuestras soluciones.
Desde el punto de vista comercial, también estamos trabajando en soluciones para ampliar el campo de posibilidades de las pequeñas empresas. A nivel de precios nos adaptamos a cada proyecto, estudiamos conjuntamente soluciones de renting para los cobots y, puesto que WETRON es una pyme certificada como innovadora por el Ministerio de Ciencia e Innovación, también podemos trabajar con las ayudas financieras destinadas a la I+D.
Además, independientemente de su tamaño, todos nuestros clientes cuentan con la garantía WECOBOTS By WETRON ®, y pueden solicitarnos fácilmente a través de nuestra web.