Industrial robots are one of the best inventions in today’s world, having numerous applications in factories, warehouses, and industries. There are multiple use cases for different robotic applications. In this article, we will help you understand the most common industrial robot applications and the different types of robots used in those particular applications. So, keep reading.
Industrial robots resemble humans, consisting of multiple joints, articulations, and manipulators that are programmable and work together to execute a specific task efficiently and quickly. Additionally, industrial robots also help to achieve cost synergies and reduce wastage.
These robots are generally motor driven and mostly offer rapid, consistent performance in heavy-duty or repetitive tasks. Hence, they are widely used in the production, manufacturing, machinery, and assembly sectors.
Automated robot parts are used in countless industries and workplaces for basic tasks. These robots are constructed using sturdy and durable metal, often steel or cast iron. As technology advances and industries develop, we will be able to see many more widespread applications of industrial robots in future.
However, in the past decade, the availability and affordability of these robots have decreased. In this context, through this article, our experts will be elaborating on the different applications of industrial robots and the types of robots used in each industrial robot application.
12 Industrial Robots Applications at a Glance
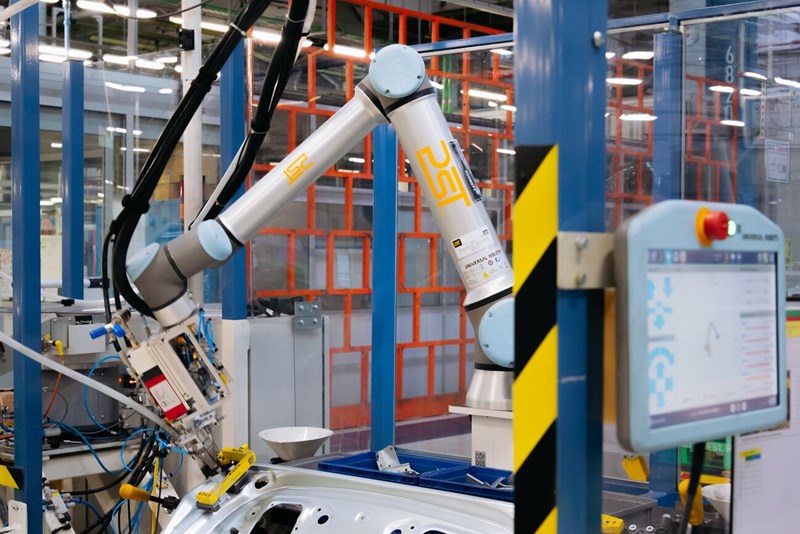
Assembly and Dispensing
A critical step in the manufacturing process is the assembly of tiny pieces into bigger ones. Until recently, only human dexterity, eyesight, and intellect could be used to complete such an assembly. Many of these duties can now be performed by robots thanks to recent technological breakthroughs. Robots that can administer bonding chemicals are a related technology since many assembly procedures need adhesives.
Assembly Robots
The auto industry was one of the earliest industries to use industrial robots for assembly. Today, uses for assembly robots extend well beyond the automobile industry. High-speed robotic assembly of microscopic parts is becoming more and more necessary. The application of robotics frequently achieves higher throughput and more precision than human labour because of its accuracy and speed.
Adhesive Dispensing Robots
Adhesives and sealants are applied by a dispensing robot in several applications. These may include using fasteners to join the components, covering the pieces with sealant, and many more techniques. A portable, quick robot is required for smaller tasks like distributing glue and epoxy. A bigger payload robot is used in larger applications, which are frequently encountered in the automobile sector.
Handling & Picking
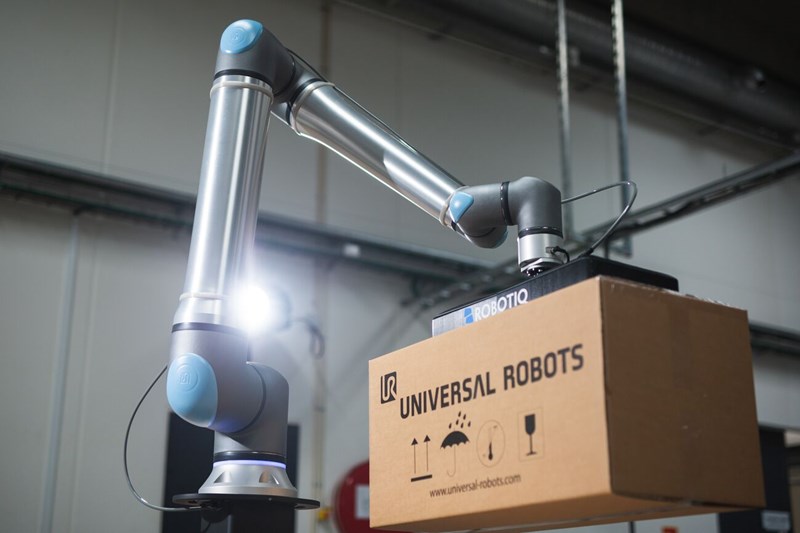
Handling and picking robots include moving objects about a warehouse or taking items out of a tote and putting them in a shipping container. Robots that can pick and fill orders are in high demand due to the growth of e-commerce.
Material Handling Robots
Forklifts that operate autonomously reduce the amount of labour needed to move products. Smaller carts are also considered autonomous mobile robots (AMRs), in addition to bigger autonomous vehicles like forklifts.
AMR is frequently used in warehouses to move items from an order picker to a packaging station. Transporting things inside a building has traditionally been accomplished using conveyor systems that employ revolving cylinders or moving belts.
Liquid Handling Robots
Applications that call for frequent, repetitive pipetting include testing medical samples, examining the chemical makeup of liquids, and conducting biological experiments. A small amount of liquid is drawn into a syringe, and precisely measured amounts are then transferred to another container through the process of pipetting. Pipetting might take hours each day for laboratory and medical workers. It's a manual, repetitive procedure where mistakes are easy to make.
Pick and Place Robots
This is maybe the most common use of robots in the manufacturing industry. These robots can load and unload processing equipment, remove components off a conveyor belt and place them in totes or shipping containers, and sort components from an unorganised state to an organised one. When there are few variables, this type of robot is typically used. For instance, the same sort of part has to be arranged, stacked, or placed into a tray as it moves down an assembly line.
Order Picking Robots
The "Holy Grail" of order picking is frequently described as fully automated robot order picking. These highly developed robots have recently become accessible. The incredible range of things the robot will encounter is the reason behind this. Transporting things inside a building has traditionally been accomplished using conveyor systems that employ revolving cylinders or moving belts.
Machining & Cutting
Robots in a manufacturing or machine tool shop setting may mechanise numerous repetitive tasks.
Machine Tending and Loading Robots
Robots used for machine tending place workpieces inside machine tools and remove them after an operation is finished. During a typical cycle, a robot arm will take a blank component off a tray, place it into the machine, wait for the process to be done, and then remove the finished part and place it on the same tray, or maybe a new one.
Milling Robots
Milling robots advance CNC automation by enabling automatic tool replacement and unsupervised operation. The application of robotics for milling increases the operation's precision and flexibility, lowers the number of faulty products, and increases worker safety. Improving the working environment can aid in keeping employees.
Drilling Robots
Both milling and drilling use End of Arm Tooling (EoAT), which rotates and cuts material from a workpiece, making them identical operations. Consequently, the two tasks are occasionally merged into a single robot. The robot arm can autonomously switch between milling and drilling tools.
Laser Cutting Robots
The material is less likely to deform when cut with a laser, and accuracy may be increased since the laser beam does not become less effective over time. Without employing lasers, it might be difficult or even impossible to cut some materials. Diamond dies were drilled with the first laser cutting device utilised in manufacturing.
Plasma Cutting Robots
Compared to more conventional "metal on metal" techniques, plasma cutting offers benefits. It makes precise cuts with a cleaner edge and doesn't produce metal chips. However, because the CNC could only move in two directions, early plasma cutting machines were typically limited to cutting sheet material. Robotic applications for plasma cutting can move with six degrees of freedom, allowing for incredibly flexible operations and the potential for cutting intricate shapes.
Waterjet Cutting Robots
As the name suggests, a water jet cutter employs a strong, high-pressure jet of water to cut a variety of materials. A high-pressure water jet is enough for softer materials like plastic, rubber, and wood. An abrasive substance can be added to the water jet to help cut through tougher objects like metal, stone, or glass. One benefit of water jet cutting is that there is no "heat-affected zone," which is crucial for particular types of materials that have a propensity to twist and distort when exposed to heat.
Welding & Soldering
With the many robot applications, many welding and soldering jobs may be automated.
Arc Welding Robots
By heating metals to their melting points using electricity, arc welding binds metal components together. The molten metals are permanently linked, and the junction is airtight when they cool. Due to the flexibility of arc welding, flat sheets, tubes, and rods may be connected, and the weld can be placed anywhere on the workpiece's surface. Robotic applications for arc welding can automate a variety of activities and have been expanding quickly.
Spot Welding Robots
Using electrodes that hold the metals together and conduct energy through the workpieces, spot welding welds relatively thin steel items. Spot welding connects two pieces of steel quickly, evenly, and effectively. In the automobile sector, applications of robotic spot welding are frequently used because it produces parts with superior quality, repeatability, and production speed compared to human welding. Also enhanced is worker safety.
MIG Welding Robots
Three components make up MIG (Metal Inert Gas) welding: heat generated by electricity, an electrode that fills the joining region, and inert gas that serves as a temporary air barrier for the weld. Since any wind will interfere with the inert gas's shielding function, MIG welding is typically not done outside. The application of robotics can automate the MIG welding procedure. Robotic MIG welding increases worker safety while lowering expenses and increasing production.
Laser Welding Robots
Workpieces are connected by laser welding using a laser beam. Because the width of the laser beam, the depth of penetration into the workpiece, the route, and the speed of the beam can all be accurately controlled, laser welding lends itself well to automation.
Soldering Robots
By inserting a melted filler substance (solder) into the junction, objects are linked together by the process of soldering. The melting point of the filler material is lower than that of the workpieces. Soldering doesn't entail melting the components to be linked as welding does.
Both smaller tabletop stations for relatively low production quantities and massive systems that can manage extremely high production rates are both examples of robotic soldering stations. Higher productivity, accuracy, and reproducibility are the results of robotic applications.
Casting & Moulding
Casting is the method of creating metallic objects by pumping liquid metal into a cavity or die that has been carved into the shape of the thing to be formed. While various kinds of materials may be utilised, moulding and casting are similar in that plastic is frequently employed. Casting often takes longer than moulding.
Die Casting Robots
Robotic arms can automatically remove the component from the die, place it into a cooling bath, remove any surplus material, and then place it on a conveyor system. Pieces emerge out of the die very hot and are often cooled by submerging them in water. Band saws are frequently used to remove extra and unnecessary material. It is safer and less taxing for the workers to have robots carry out these tasks. Both productivity and throughput have improved.
Injection Moulding Robots
Robotic automation of injection moulding entails taking the final product out of the mould, clipping off any superfluous material, throwing it away, and setting it on a conveyor or container. Much like in die casting, robotic applications are used in the injection moulding process to promote productivity and safety.
Finishing & Sanding
Drilling, casting, die casting, and welding are just a few industrial procedures that can leave behind undesirable material or produce ragged or sharp edges. To produce the intended finished product, this undesirable material must be eliminated. Sanding and finishing are the tasks at hand.
Deburring Robots
Unwanted material is removed from a workpiece during deburring, often using spinning bits that are specifically shaped. In a deburring process, the workpiece is typically stationary while the deburring machine rotates around it. Manual deburring is dull, repetitious, and exhausting. Robotic deburring is quicker, more accurate, and more reproducible than hand deburring and does not wear out the operator.
Grinding Robots
A part's excess or undesirable material is removed during industrial grinding processes. In the majority of grinding applications, the grinding machine is fixed, and the component or workpiece is moved while coming into contact with the grinding surface at various angles and with the proper amount of pressure to produce the required results. Grinding activities are consistently, correctly, and continuously carried out by robot arms.
Polishing Robots
Smooth or glossy surfaces are produced by polishing procedures. When polishing a smooth piece of metal or plastic, for instance, a soft cloth or polishing disc may be used. In other instances, abrasive materials with coarse grains that get finer are used to polish objects like glass and stone. Robotic polishing can repeat movements accurately and quantify the force used to provide consistent, high-quality results.
Painting & Coating
Applying paint or other coatings to a workpiece is known as industrial painting and coating. The painting and coating procedures are quite repetitious since the component that has to be painted or coated in production has a clearly defined shape and size.
Therefore, industrial robot applications are a good fit for painting and coating activities. The machines can operate constantly with no pauses and no downtime aside from routine maintenance, producing consistent, high-quality products. Robotics improves safety by removing the need for employees to breathe hazardous gases or overspray.
Painting Robots
Robots that may be utilised in building or home improvement projects are recent additions to the area of painting robotics. While some require an external power source and use a hose to deliver paint, others are battery-powered and made to function in the new building. Robotic painting can produce more uniform results while being up to 30 times faster than manual painting.
Spray Painting Robots
To prevent runs and drips, industrial painting robots can precisely control the distance between the spray head and the workpiece as well as the pace at which the spray nozzle moves. To achieve consistent outcomes, pressure and flow must be precisely regulated. Industrial painting robots complete all of this with a high level of excellence.
Coating Robots
Because robotic movement can be accurately controlled, coating operations may be automated using robots. In comparison to manual procedures, robots are faster, more accurate, and more consistent.
Cleaning & Hygiene
For the sake of the finished product's quality as well as the health and safety of those who work there, industrial facilities must be kept clean. Cleaning is a tedious and frequently repeated procedure. Industrial robot applications for cleaning are therefore becoming more and more common.
Cleaning Robots
Cleaning of commercial floors Robots are capable of independently moving around a building and scrubbing the floors. They feature sensors to help them avoid people, forklifts, furniture, and other obstacles, as well as an internal map of the area they need to move across and clean.
Disinfection Robots
Commercially available autonomous mobile robots for surface sanitation. They can go through corridors without incident and are intelligent enough to avoid running into people or other moving objects. Some robots carry cleaning solutions and make physical touch surfaces using a robotic arm. Other cleaning robots cleanse surfaces by exposing them to ultraviolet (UV) radiation.
Industrial Robot Vacuums
Industrial robot vacuums can be used to autonomously remove dust and debris from industrial facilities. Some models have a chute or receptacle where the robot may automatically release the dirt it has gathered. Using industrial robot vacuums has several benefits, including lower labour costs and thorough, reliable, and consistent cleaning.
Logistics & Storage
Warehouse Robots
Order picking, packing, sorting, labelling, and transportation are just a few of the many operations that may be automated by robots working in a warehouse or distribution centre. More than 80% of warehouses are anticipated to not utilise automation or robotics by 2021.
This will probably change very fast. The fastest-growing kinds of robots for the movement of items inside a warehouse or distribution centre are automated guided vehicles (AGVs) and autonomous mobile robots (AMRs).
Delivery Robots
Commercially, delivery robots come in many different configurations, sizes, and purposes. Some delivery robots have the appearance of wheeled carts and are used to distribute meals in urban settings. Other delivery robots resemble people because they stand on two legs, have arms, and have a dome-shaped dome in place of the head. They also have two legs and arms.
Robotic unmanned aerial vehicles (UAVs) are available to deliver products to customers and leave them there. Additionally, there are robots with four legs that resemble dogs that deliver packages. There are just a few places where self-driving cars are being used as delivery robots. In any situation, delivery robots have various benefits, such as quick delivery, cheaper labour, and dependability.
Packing & Palletizing
Manufacturing, warehouses, and distribution facilities all perform the tasks of packing and palletizing. The packing and palletizing processes become more repetitious as the trend toward smaller items persists. The health and safety of the workforce may be adversely affected by this. Industrial robot applications boost productivity and help guard workers from workplace accidents.
Packaging Robots
Packaging robots can autonomously produce boxes in a variety of sizes as needed. As an illustration of one use, packing robots may autonomously insert big wire spools into boxes, inserting the bottom plastic shipping cap first and the top cap last, before sealing the box and labelling it for delivery.
Palletizing Robots
Boxes and containers may be stacked neatly and efficiently on a pallet using palletizing robots. Artificial intelligence may be used to arrange the boxes so that the heavier ones are placed on the bottom when there are several different goods inside.
The boxes may be arranged to accommodate as many as possible on the pallet by changing their orientation. Palletizing robots may also automate shrink-wrapping the entire pallet in plastic to stabilise it for shipment.
Inspection & Quality Control
Some quality control concerns are life and death because a faulty part or an improperly placed part may result in a scenario that puts the user's life in danger. Often, the human examination is only 80% correct. Industrial robot applications have the potential to be 100% accurate.
Vision Robots
Vision robots may check a variety of qualities, including the presence of fractures, measuring of dimensions, and coating uniformity. There are underwater robots for checking oil rigs and salvaging operations, and inspection robots that can move down a pipeline for the oil and gas sector. Drones that fly in the air may survey roofs and other high spots.
Harvesting
Harvesting of fruits and vegetables is very critical and must be done at the proper time to ensure that they are of high-quality and are capable of reaching the customers without any wastage or spoilage. Similarly, the harvesting of grains and other crops is also sensitive to time and labour. Therefore, human labour must be replaced with robotic applications to achieve efficiencies.
Harvesting Robots
These robots are equipped with soft grippers, which makes them capable of handling fragile crops without causing any damage. They also have special vision systems that help them determine whether a piece is ripe or not. These robots increase the efficiency of the process and reduce labour costs, relieving factory owners from uncomfortable labour.
How To Find The Right Type Of Robotic Arm For Your Task?
To choose the perfect robot for your needs, there are several factors that you should keep in mind, as mentioned below.
Industrial Robot Applications
Firstly, define the application for which you need a robot. If you are looking for a compact pick and place application of a robot, you must choose a SCARA robot. At the same time, if you are looking for an application for a robot for placing small objects at a faster rate, go for a delta robot.
If you want your robot to work alongside your factory labourers, collaborative robots should be your choice. Therefore, it is imperative to understand the application of the robot that you are choosing.
Robot Payload
Payload refers to the maximum load the robot can carry in the working space. Incorporate a part weight or a robot gripper weight into the payload if you are looking to carry the part from one machine to another.
Number of Axes
The number of axes in a robot defines the degree of freedom the robot has. For straightforward applications, a simple four-axis robot is more than enough. However, if the robotic application is for a small workspace with a lot of twists and turns, a six or seven-axis robot must do the work. Having multiple axes offers greater flexibility.
Industrial Robot Reach
It is essential to understand the maximum reach of a robot during any robotic application. The lowest point generally measures the maximum vertical reach a robot can achieve and the maximum height the wrist can reach.
The maximal horizontal reach refers to the farthest point that the wrist can reach horizontally from the centre of the robot base. These specifications are different from one robot to another and can be a limiting factor. Therefore, choose wisely.
Repeatability
Another factor that affects the application of a robot is repeatability, that is, the robot's capacity to reach the same position every time. Mostly, robots can repeat within 0.5 mm or sometimes even more. For example, the robot must be super repeatable for building an electric circuit board. However, if the robotic application is quite rough, the industrial robot does not require that level of precision.
Speed
Speed as a user-specific criterion. It refers to the rate at which the job needs to be done. The sheet of specifications generally mentioned the maximum speed, but you should understand that the robot's speed can be anywhere between 0 and maximum. The unit in which it is degrees per second. Some manufacturers also tell their customers the maximum acceleration rate.
Brakes
Another important consideration should be the braking system of the robot. Some robots have brakes, while others don’t. To achieve a precise task, there should be a sufficient number of brakes. At the same time, look at the inertia and torque that are offered by certain robot segments. If these are incorrect, the robot might shut down because of overload.
IP Rating
Depending upon the location that you want your robot to work in, you must achieve an IP rating. Robots working in the manufacturing sector and for laboratory purposes will have different IP ratings. Checking the IP rating is an international norm and, hence, it is always advisable to comply with it.
The Future Of The Applications Of Robots In Industries
In today's world, robots are less about mechanical size and structure. They are more like data collectors. Traditionally, robots used to work separately in their world. But today, they are integrated into the workforce. Similarly, traditional robots were only used for specific tasks at particular locations.
However, today we see collaborative applications of robots in industries. These co-bots work alongside factory operators and have multiple sensors that make it possible for them to operate in an environment full of people and records. As a result, there is useful traceability and detailed data analysis, which helps in an efficient decision-making process for the future.
Advances in robotic technology allow us to take these robots into laboratories, retail shops, floor work operations, and more. Ahold Delhaize is an autonomous robot introduction which is designed to improve store operations.
It is equipped with several sensors, navigation systems, cameras, and much more that help the robot work alongside employees and scan floors for hazardous conditions. This robot can also keep a record of missing, misplaced, or mispriced inventory. In the future, we can expect autonomous robots to work on all the parts of retail, i.e., from warehousing to delivery.
In other industries, for example, agriculture, the use of robots is in the form of robotic drones that can examine the deficiencies in crops. These drones are also capable of analysing the water and the dryness level. Mobile robots and drones are capable of monitoring oil and gas pipelines and electric transmission systems.
All in all, robots are meant to do mundane, monotonous, and time-consuming tasks. With the advancement of AI, the robotic industry is changing dynamically. But, it still has at least a decade in the future. The robotics industry is just the beginning.