A manipulator robot is made up of links joined together by joints, and these linkages form a kinematic chain. The end effector, which is similar to the human hand, is the functional end of the manipulator's kinematic chain.
A gripper or an end effector with the ability to weld, paint, assemble, etc., can be used as the end effector. In this article, our experts will help you understand a robotic arm design - both the mechanical arm design and the electronic arm design. So, keep reading.
Robotics is the study, development, and use of robotic systems in production. The design of the robotic arm is created to assist various sectors in doing a job or work instead of employing human labour as manufacturing industry activities increase. Robots are typically used to carry out unpleasant, risky, excessively repetitive, and harmful activities.
Material handling, assembly, arc welding, resistance welding, machine tool load and unload functions, painting, spraying, and other tasks can all be done by robots. It is incredibly helpful since it does tasks with greater intellect, precision, and energy than humans do.
For instance, a robotic arm is frequently used in assembly or packaging lines to lift tiny things repeatedly, a task that would be too taxing for a person to perform for an extended length of time. The robotic arm can efficiently and quickly perform the light material lifting operation since it is not hampered by human weariness or health hazards.
What Is a Robotic Arm?
A robotic arm is a device constructed of linkages connected by appropriate joints so that it may move in space and with the degrees of freedom needed for the task at hand. Frequently, the robotic manipulator may be trained to do specific tasks. It is additionally referred to as anthropomorphic because of how close in function it is to a human hand.
The optimum robotics arm design reduces the product cycle time and cost since it boosts a robotic arm's efficiency and speed of operation by being able to duplicate the outcomes with a little mistake. The danger of damage is also significantly lower when there is no human involvement, making it simpler to handle hazardous materials.
6 Main Types Of Robotic Arm Designs
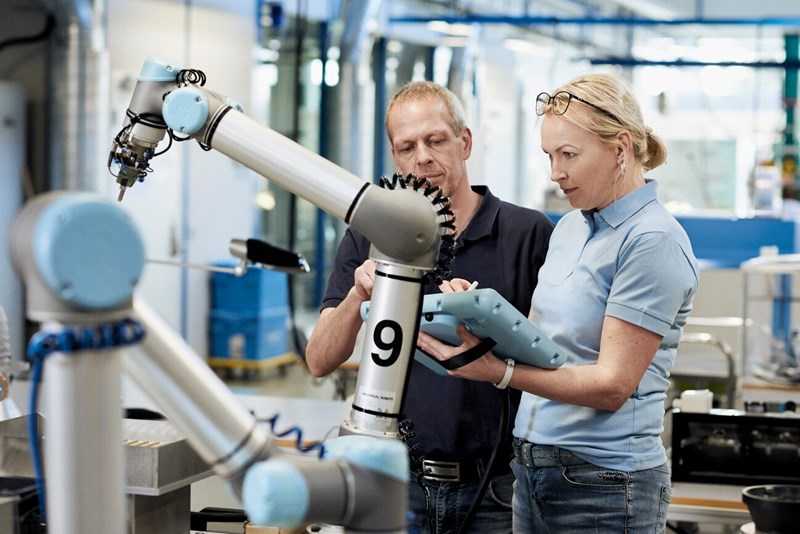
Cartesian Robot/Gantry Robot
This arm is made of three joints that are capable of being manipulated to make spatial movements. This type of robot may be used for a variety of tasks, including pick-and-place labour, operating machine equipment, arc welding, applying sealants, and assembly tasks.
Cylindrical Robot
This robot's axes are configured on a cylindrical coordinate system. Some typical uses include spot welding, managing machine tools, product assembly, and handling die-cast or other machines
Spherical Robot/Polar Robot
This kind of robot forms the polar coordinate system with its axes and is usually employed in gas, arc, and spot welding operations, die-casting mechanisms, and handling machine tools.
SCARA Robot
SCARA refers to Selective Compliance Assembly Robot Arm. It is particularly helpful for tiny robotic assembly processes. As its name implies, it has two parallel rotary joints that offer compliance in one place, while it is stiff in the other two. It manages the use of machine tools, the application of sealant, assembly processes, and pick-and-place activities.
Articulated Robot
This robot usually has three or more rotary joints in its arm. It can be used for dying, casting, gas & arc welding, spray painting, fettling equipment, and assembly processes.
Parallel Robot
A robot that has parallel rotary or prismatic joints. Robots of this kind are employed in optical fibre alignment and cockpit flight simulators.
The Different Components Of Robotic Arm Design
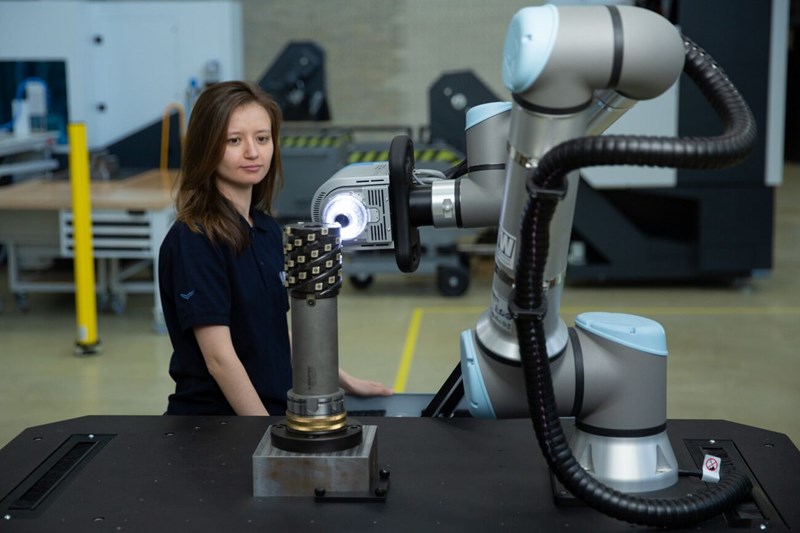
Base
One of the most crucial components of the robotic arm is its base. Because it serves as the foundation for the robotic arm, it is affected by the weight of all the other components, as well as the payload. The robotic arm base is equipped with a servo motor that works with the rotating shaft.
Forearm
The forearm determines the robot's range and moves more compared to the other components. The joint formed here is based on the elbow in the human arm, and similarly, its primary function is to support the weight that the arm is lifting.
The shaft situated between the elbow and forearm joint serves as the arm's power source. Between this connection and the link with the base, the robot arm has a minimum angle of 130 degrees and a maximum angle of 160 degrees.
Shoulder
The shoulder joins with the rotating shaft and gives the robotic arm its rotational motion. This component has a shaft and key combination that is connected to the bottom. This is the section that transmits the rotating motion from the power source to the upper body of the robot arm.
Biceps
Much like the muscles in the human arm, the robot’s biceps move less than the forearm, but gives the forearm and wrist strength and stability. Its upper end has a shaft that allows it to revolve around the axis of the shoulder-elbow joint.
This component's base has holes and a space between two expanded grooves where the wrist-creating joint 3 can be positioned. The shaft at the apex of the elbow is joined to the power source. The end of this part of the arm is where it rotates.
Wrist
The robotic arm's wrist connects the forearm and the end effector and ensures the end effector’s precision. On the axis, it may revolve 360 degrees. However, the wrist's rotation can be limited because the robot's base itself rotates. The degree of rotation may be changed depending on the user's needs.
End Effector
The end effector, also known as end-of-arm tooling, is a gadget or tool that is attached to the end of a robotic arm, and which interacts with the robot’s assigned task. The design of an end effector, as well as the hardware and software that operate it, is dependent on the robot’s task or application.
Servo Motor
The angular or linear position, velocity, and acceleration may be precisely controlled with a servo motor, a rotary or linear actuator. It comprises an appropriate motor connected to a position feedback sensor. It also needs a rather complex controller, frequently a special module created just for use with servomotors.
There are different ways that cobots are constructed from base to forearm, that determine it's flexibility. For example, UR cobots have 6 joints where 3 of them used in base, shoulder & elbow and other 3 are in wrist, which gives a lot more flexibility compared to robots with just 2 joints in wrist.
What Is Meant By Robotic Arm Design?
Mechanical Design of Robotic Arm
The mechanical design of a robotic arm, which was inspired by the human hand, consists of several connections that together comprise a kinematic chain. The joints that connect the links provide the system with its rotational and translational movement capabilities. An end effector is also usually added to the end of the wrist-joint where a human hand would be on a human arm.
Degrees of Freedom
In robotics arm design, the degree of freedom (DoF) of a robot is calculated by subtracting the number of constraints on its mobility from the total number of freedoms of the rigid body. The joints are usually the reason for these mobility restrictions.
Examples of joints that only allow one degree of freedom between the two bodies they link are revolute and prismatic joints. Joints that have more than one degree of freedom include spherical joints that have three relative degrees of space and universal joints that have two.
A robotic arm can be described by its degree of freedom. A bigger number indicates increased flexibility in aligning a tool, making it a significant parameter for robotic arm design. Take the case of a serial robot, where the number often refers to the number of single-axis rotating joints in the arm.
The end effector is positioned with five degrees of freedom in serial and parallel manipulator systems, consisting of three translational DoF and two for orientation. Thus, a direct relationship between actuator position and manipulator setup may be found.
Robot Workspace
The collection of all places that the end effector can reach is the robot workspace, sometimes referred to as accessible space. The link lengths, rotational and translational restrictions, the general design of the mechanism, and other factors all affect the workspace. By altering the connection lengths and permitted degrees of freedom for the mechanism, the work volume produced in this way specifies the usable space for the robot.
Electronics Design of Robotic Arm
Servo Motor Control
Servos can be either AD (battery-driven) or DC (input power source) motors. Servo motors often offer excellent torque to inertia ratios thanks to an internal gearing arrangement. Due to the feedback control loop, accuracy is relatively high.
Small and portable DC servo motors are popular for use in toys, educational robotic applications, and RC planes. Servo motors typically have a rotational limit of between 90 and 180 degrees. However, certain motors can provide more angular motion.
Due to their ability to deliver a high degree of spatial orientation precision, servo motors are an excellent choice for use in robot arms and legs, rack and pinion steering, and sensor scanners. Since these servos are entirely self-contained, setting up the velocity and angle control loops is straightforward.
Servo Wiring
Servo motors typically have three wires: The colour of the ground—black or brown—identifies it. "Red" serves to identify power. Signal wire can be distinguished by its yellow, orange, or white colour (3-5V).
Servo Voltage (Red and Black/Brown wires): The average working voltage range for servo motors is 4.8 to 6 volts. While certain Hitec servo motors are also available that work at a greater rated voltage, most micro-sized servo motors run at a lower voltage.
Signal Wire (Yellow/Orange/White wire): The black and red wires supply the servo motor with electricity, but the signal wire transmits the commands used to control the servo. A logic square wave of a certain wavelength (often 50 Hz) is typically transmitted to the servo, which causes it to be oriented at a given angle because the wavelength precisely corresponds to the servo angle. For instance, the Arduino Mega receives i/ps from the PC to produce a square wave, which then regulates the servomotor's angular direction.
Microcontroller (Basic Concept of Arduino)
Servo motors use microcontrollers to regulate their accuracy and angular position. One example is the single-board microcontroller, an Arduino, which can be configured to suit the application. It has on-board I/O structures, and USB power connectors, and is designed for an Atmel AVR CPU.
Robotic Arm Control: How to Control a Robot Arm?
The robotic arms may be capable of autonomous operation or human control. In manual mode, a trained operator (programmer) instructs a robot to complete its mission and utilises a transportable control tool (a teach pendant) to do the operation. This process moves along really slowly.
The multi-level control configuration of a standard robotic arm consists of a microcontroller, driver, and a computer-based user interface. Inverse kinematics ideas are utilised to provide programming and control system flexibility. Manual mode can also be used to do this. A common microcontroller has a programming/development board attached to it.
How To Pick The Right End-Effector?
An end effector in robotics is a tool or device attached to the end of a robot arm, in place of the hand. The robot's end effector is the component that interacts with the outside world. The design of an end effector, as well as the hardware and software that power it, is dependent on the task that the robot is performing.
There are many different uses for robots for which an end effector must be chosen. It could be a welding interface to hold the electrodes or a hand-like gripper designed for pick and place operations in a specific area, as seen below.
The manipulator, which is the most important component of the robotic arm, can have an interface similar to a spray paint pistol for painting or a platform for simulations. Pneumatic, electrical, or hydraulic end effectors are all possible. Servo motors are typically used to drive the end effectors.
Conclusion
The delivery of the sheet from the stack to the shearing machine is the primary justification for choosing to develop a robotic arm. The shearing machine and the stack of sheets are situated close to one another. Any other mode of transportation, such as a linear robot, cannot be employed since they are so close together. The pick and place mechanism's robotic arm has been successfully designed.