Robotic welding is a process that helps the industrial sector to automate its processes, increase accuracy, enhance safety and reduce lead time. The robot welding process is considered to be the most productive when it is implemented for high-volume and repetitive tasks. There are multiple types of robotic welding processes. In this article, we will go through each of them in detail and understand their benefits and applications. Read on to learn more!
When a welding process is automated using robots, we call it robotic welding. These building robots perform and manage welding tasks based on the program and are capable of being reprogrammed as per the intended project. However, this does not eliminate human intervention as welders still control and supervise the welding robots.
Welding robots bring many benefits to the manufacturing process, including precise results, less wastage, and improved safety. These robots can reach locations that are inaccessible by human hands and perform complicated tasks much more precisely. Therefore, the time taken in the manufacturing process is minimised and greater flexibility is achieved.
There are different types of robotic welding available on the market, and the main focus should be on choosing the correct welding program for a long-lasting and durable impact. Through this article, we hope you will be able to understand the entire process better for informed decision-making.
What Is Robotic Welding?
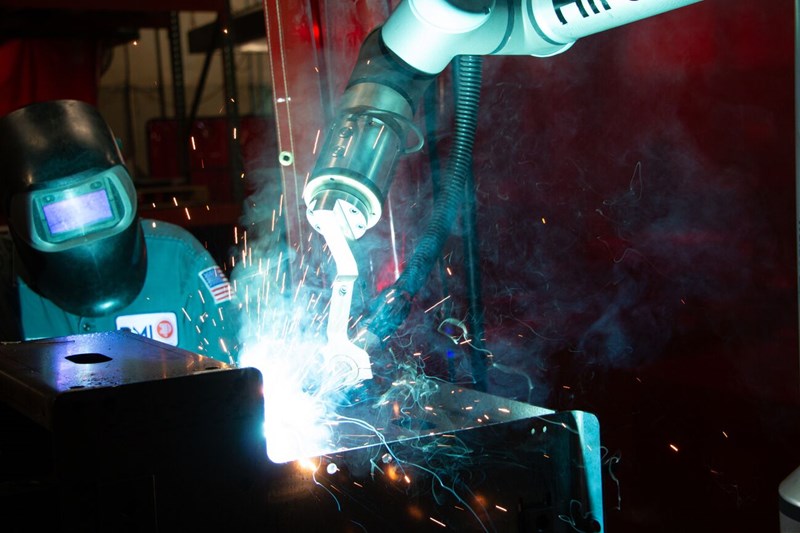
Robotic welding is an automated welding technique that is performed by a welding robot, which is a special type of industrial robot. Welding robots are typically stationary and are used to repeatedly perform the same welding operation. An industrial robot is a programmable, multipurpose manipulator designed to move material, parts, tools, or specialized devices through varied programmed motions for the purposes of loading, unloading, assembling, material handling, machine loading/unloading and other manufacturing operations. They are used in assembly lines and other manufacturing applications; wherever materials need to be handled.
Robot welding was first introduced in the industrial sector during the 1960s. In most cases, building robots are used for resistance welding and arc welding in heavy industries, such as the automobile.
There are multiple ways in which robots work - a pre-programmed position, machine vision, or a combination of both. However, the most significant benefits of robot welding and its technology have been the increase in accuracy, repeatability, and throughput
An Insight Into The Robotic Welding Process: How Does Robotic Welding Work?
Robots are often thought of as being synonymous with automation. Welding robots, in particular, incorporate an arm that is capable of moving in three dimensions and welding metals together. There is a wire feeder that sends a filler wire to the robot, and a high-heat torch towards the end of the arm that melts metals during the welding process.
Some certified human operators are employed to maintain these robots and give them instructions. There is a control box, which the operator uses to control the robot’s programs, and an operation box that helps to start the operation.
The robotic arm's tool warms up to melt metal and connect the components. A wire feeder supplies extra metal wire to the arm and torch as needed. When it's time to weld the next portion, the arm moves the torch to the cleaner to clear any metal splatters off the arm that may otherwise freeze in place. Moreover, there are arc shields which are capable of preventing the high heat arc from mixing with the oxygen to protect the workers and the nearby locations.
The 7 Most Common Types of Robotic Welding Processes
Welding is an art as well as a science that requires a high level of training. However, there are quite a few professionals who are unable to meet these qualifications. Therefore, in today's world, robotic automation is the new normal. There is a wide range of machinery available and robots adapt to a variety of welding processes, including:
Arc Welding
The arc method is one of the most common forms of robotic welding. An electric arc produces high heat, up to 6,500 degrees Fahrenheit, which melts the metal in this process. Molten metal joins parts together, which solidifies into a secure bond after cooling. When a project necessitates a vast number of precisely linked metals, arc welding is a great option.
Resistance Welding
Robots may employ resistance welding when tasks require heat treatment or a cost-cutting measure. A stream of electricity forms a pool of molten metal as it flows between the two metal bases throughout this operation. This molten metal is what holds the metal components together.
Spot Welding
Some materials are resistant to electrical currents, making them unsuitable for other types of welding. This is a common occurrence in the automotive industry while putting together sections of a vehicle's body. Robotic welders solve the problem by joining two thin metal sheets in a single area using a version of resistance welding.
TIG Welding
TIG welding may be required for robot welding applications that need a high level of accuracy. Gas tungsten arc welding, or GTAW, is another name for this technique. An electric arc forms between a tungsten electrode and the metal base.
MIG Welding
Gas metal arc welding, often known as GMAW or MIG, is a simple and quick process that produces a lot of deposition. A wire is repeatedly moved to the welder's heated tip, which melts it and allows a considerable amount of molten metal to drip onto the base for attaching it to another component.
Laser Welding
Laser welding is the ideal method of metal joining for projects that demand precision for a large number of pieces. Laser welding is frequently used on small pieces, such as jewellery or medical components.
Plasma Welding
Because the operator may quickly modify both the speed of gas travelling through the nozzle and the temperature, plasma welding provides the most versatility.
Robotic Welding vs. Manual Welding: Which Is Better?
In today's production, manual welding still has a place. Manual welding is the ideal option for tasks that require an expert to swiftly modify the welding methods employed. Professional welders can swiftly adjust what they're doing, while robots are slower to adapt to new scenarios.
Professional welders will not go away anytime soon since hand welding is still a procedure that many businesses require. Indeed, given the above-mentioned lack of skilled welders, people with certification will have little trouble finding work, even if various enterprises invest in robots.
Amazon Web Services will not be forced out of the certification industry by replacing hand welders with robots. The majority of robot welder operators must be certified on the robotics side of the industry, which Amazon Web Services also offers. The presence of welding-experienced robotics professionals guarantees that projects are correctly planned to be completed as swiftly and cost-effectively as possible.
The 5 Key Advantages Of Robotic Welding For Manufacturers
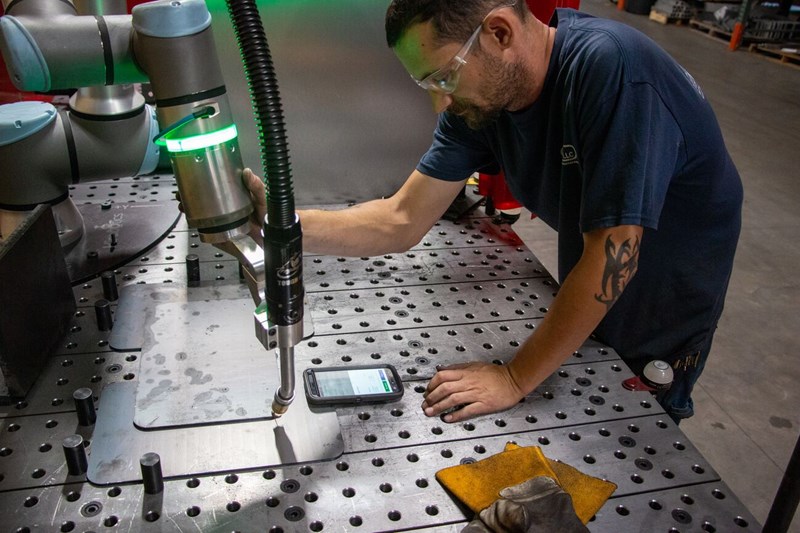
Robotic welding is gaining popularity among job shops and contract manufacturers because it provides the following benefits:
1. Limited Human Efforts
Human welders are expensive to hire, train, and retain. Instead of having to locate and educate them, you may optimise your personnel by having one exceptional welder supervise the operation of numerous automated cells using a robotic welder.
2. Higher Productivity
Welder turnover may be reduced by automating the placement of the same high-quality welds in the same locations again and over again with minimum human error, reducing repetitive and dull activities.
3. Lesser Wastage
Welding robots may be exceedingly accurate, resulting in fewer weld spatters and cleaner seams.
4. Lesser Costs
With robotic welding, filler material and weld wire are utilised more efficiently and wastefully, lowering the overall cost of the product.
5. Time-Efficient
With predictable component placement and procedures configured for the robotic welder, parts travel through the system more rapidly, potentially allowing for improved output.
Real-Life Applications of Robotic Welding
Robotic welding has grown manifolds in recent times, especially in metal and heavy sectors. It is more often incorporated in industries that use spot and laser welding, as it results in time-saving and higher productivity.
Robotic welding is suitable for short welding processes and repetitive action items that don't require continuous oversight, adjustments, and alterations.
Some robots may also be used for long welding processes, such as in the shipbuilding sector. This is because these robots facilitate external axes.
Robotic welding is widely employed in mass production activities where efficiency and quantity are critical. These robots are programmable as per the requirements. Robots can also be used for smaller and one-off manufacturing processes, too, in a cost-effective manner.
The Future of Robotic Welding
Currently, robotic welding is used only on a small portion of building projects. However, with emerging technologies, the trend is likely to change. Future innovations will develop much more interactive welding robots, such as:
1. Mind-Controlled Welding Robots
Currently, operators must program welding robots to start them on a process. Operators must now program welding robots before they can begin a procedure. Future operators may simply have to think about what they want the robot to perform instead of using a computer interface or instructional pendant.
Researchers have developed a headgear that converts brain signals into robotic welding arm motions. If used in industry, this method might reduce the amount of training required for existing manual welders to become robotic operators.
Instead of using a computer program, professionals may put on a cap and check through designs to teach the robot how to correctly weld the components together. This technology, on the other hand, is unlikely to materialise anytime soon.
2. Collaborative Robots
Prototypes are already used for collaborative robots. These devices feature a user-friendly design that allows for simple human interaction. Sensors enable these robots to acquire data and respond to changing circumstances.
To do large-scale operations, industrial robots have historically required previous programming. These long-lasting, but costly and inconvenient gadgets take up much too much room and money to be viable solutions for small enterprises.
Engineers have developed increasingly durable collaborative robots that can operate with humans in industrial settings to overcome this challenge. To assist human welders, collaborative robots might be included in manual welding areas.
Conclusion
The process of welding has evolved over the years. The traditional process of welding requires a lot of manpower, time, and cost. Robotic welding has come up to seek solutions to all these problems. Many automobile manufacturers are now using robotic welding in their production lines. The process of robotic welding is a very quick process. It is also very precise and accurate. The process is also safer than the traditional welding process. This has made the process of robotic welding very popular in the industrial sector.