Most robots are designed for heavy, dangerous, and repetitive tasks to achieve perfection and cut down on costs. A robotic arm is a machine programmed and designed to perform specific tasks efficiently and precisely. The work of a robotic arm is mostly driven by a motor and is used in different industrial sectors. In this article, we will be elaborating on the workings of a robotic arm.
A robotic arm may be one of the main parts of an industrial robot and is a programmable mechanical arm that can perform a variety of tasks. It contains several attachments through joints known as axes. Every attachment has a stepper or a servo motor that moves in a specific motion.
The greater the number of joints or axes, the greater the range of motion. These motorised axes help the robot operate with precise movements for better accuracy.
The industrial robot is moved into position so it can reach workpieces by articulating robotic arms. A six-axis robotic arm can move in six distinct directions for increased versatility.
The area that each robotic arm may use for operations is referred to as its "work envelope." Robotic arms also control the end-effector. The robotic arm positions itself to access workpieces during operation and then uses the end-effector to finish a task.
Robotic arms also need to be programmed to carry out manufacturing tasks. Usually, a controller and a teaching pendant are used for this. Manual motion can be used to program some robotic arms. In the next section, we provide you with better insights into the workings of a robotic arm.
An Insight Into The Working Of Robotic Arm
Robotic arms refer to a metal arm, usually made up of 4 to 6 joints, and can be used for several manufacturing applications. They closely resemble a human arm, having a wrist, forearm, elbow, and shoulder. The different joints allow them the required degrees of freedom of movement.
The industrial robotic arm is composed of steel or cast iron. It is constructed from the base up to the wrist. A robotic controller rotates each joint's associated motor. Hydraulic and pneumatic systems are utilised to power some of the bigger arms that are used to carry hefty weights.
The arm's function is to move the end effector, which may be used to pick up, lay down, remove, or weld a component or the complete workpiece. Depending on the manufacturer's requirements, these robotic arms can be programmed to do a variety of tasks or a single task.
These robotic arms are used for little tasks in addition to lifting large objects, palletising hefty goods, and welding complete automobiles together. Even the smallest motherboard or microprocessor may be pieced together with the precision and accuracy of a robotic arm.
These metal wonders will keep on working in manufacturing for many years to come.
The Use Of Joints In The Working Of Robotic Arm
Since robotic arms were created with the human arm in mind, we usually see them with multiple joints, allowing them the freedom to move and flexibility. Joints are any moveable portions of the robotic arm.
Each joint operates independently while also forming a seamless team with the others for maximum operation. This is how a robotic arm can move up and down while rotating at the same time. In a nutshell, a robotic arm cannot function without joints, and an industrial robotic arm must contain at least two joints.
The manoeuvrability of the robotic arm increases with the number of joints. These joints—often referred to as axes—are crucial to defining how a robotic arm will function. Joints permit freedom of movement and make a robot exceedingly adaptable.
- Joints provide a structure which makes it simple to maintain and repair. Instead of making educated assumptions, it is simple to trace a failure down to a joint once it manifests.
- Joints are flexible, allowing the robotic arms to twist, turn, and move up and down.
The Different Configurations Of Robotic Arms
Many factors need to be considered when choosing an industrial robot, including its purpose, required speed, level of precision, and whether it will function in a collaborative environment. All of these factors, and many more, are combined to determine the finest industrial robot for a job. The robot's setup is one of the key elements that govern how an industrial robot moves and restricts its workspace. Cartesian, cylindrical, spherical, SCARA, and Delta are the six main types of robot configurations.
Robot Configuration
|
Explanation
|
Common Uses
|
Cartesian
|
Robots that follow each of the Cartesian coordinates in a straight line (x, y, z). It has a work envelope that resembles a box and can be swept away using this setup.
|
The print nozzles of many 3D printers are arranged in a Cartesian fashion.
|
Cylindrical
|
It permits the tool it uses to revolve along a central axis. The tool may also travel up and down the centre axis, as well as in both directions toward and away from it. With this arrangement, a cylinder-shaped work volume is produced.
|
This set-up is frequently used for spot welding, handling die-cast machines and machine tools, and assembly tasks.
|
Spherical
|
This arrangement produces a tool action that sweeps out a workspace with a sphere-like form. It allows the tool to revolve around a primary axis and a second axis that is positioned at a 90-degree angle to the main axis. The tool can also pivot around an axis.
|
They are frequently employed in material handling, welding, and die casting.
|
Selective Compliance Articulated Robot Arm (SCARA)
|
It uses pivot points to enable its tool to move in both cylindrical and Cartesian movements. This enables the tool to move more swiftly and with more ease while making particular motions, like an arc.
|
SCARA robots are utilised in biomedical applications, assembling, and palletising.
|
Articulated
|
The image of an industrial robot that comes to mind when the term is used most frequently is this one. It must have a wrist joint, an elbow joint, and at least one shoulder joint. Both main and minor axes can be included in many of these setup instances.
|
A few common uses for articulated robots include packing, arc welding, material handling, and machine tending. An illustration of an articulated setup is the VEX V5 Workcell.
|
Delta (Parallel)
|
It is the robot configuration type that can move its tool the quickest. To enable its tool to swiftly sweep out its workspace, it employs parallel connections.
|
A Delta can do various tasks, including picking and placing objects rapidly and nimbly in a sorting activity.
|
What Is The Work Envelope Of A Robotic Arm?
It is a geometrically shaped area where the manipulator robot may work. It depends on the number of degrees of freedom, size, kind, and range of end effects of the robot, as well as any parts of the robot that may interact with the environment, like a claw, for instance. The number of linear or angular actuators determines the form of the envelope.
The work envelope determines the ideal use for the robot. The size and form of the work envelope at the operating site must be specified when selecting or designing a robot for a task. To prevent mishaps, the envelope may occasionally need to be constrained by sensors that alert the controller.
How Do Robotic Arms Control End Effectors?
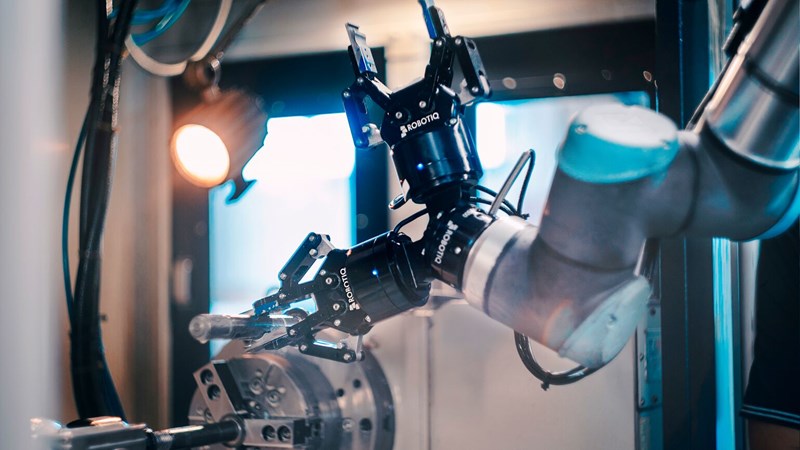
A bodily component that activates in response to a stimulus. In robotics, it is a tool used to manipulate things at the end of a robotic arm. The end effector, often referred to as end-of-arm tooling, is located at the end of the robot arm and only moves when a user activates it using the corresponding software.
To put it another way, the end effector is the one which pick and places items, puts product components together, stacks cartons and packages, etc. A robotic arm is required to automate and improve a process, but the end effector allows the robot to work. Different end effectors are suitable for various purposes, and the choice of end effectors depends on the task at hand.
How Do Robotic Arms Perform Manufacturing Applications?
Industrial robotic arms have the flexibility to handle a variety of applications, from the simplest to the most complicated tasks in the safest or harshest conditions. This is one of its main advantages. In addition to removing human workers from potentially dangerous circumstances, automating these kinds of operations frees up such personnel to perform high-value duties like interacting with clients. The following are some of the most widespread applications for robotic arms in manufacturing today:
Palletizing
Automating the process of loading items or products onto pallets is possible using robotic arms. Palletizing becomes more precise, economical, and predictable when it is automated. Robotic arms provide for the freedom of human employees from dangerous jobs that might result in physical harm.
Material Handling
By ensuring that products and materials are appropriately kept, accessible, or delivered in the right way, material-handling robotic arms may aid in the creation of a secure and effective warehouse. Automating these procedures can increase a facility's productivity, speed up the delivery of items to consumers, and reduce worker injuries.
Welding
Robots are capable of welding in high-tech industrial situations like the production of automobiles. Welding is a great option for sophisticated robots to explain why the vision and AI augmentation has a crucial influence on product quality.
Inspection
It takes longer to identify manufacturing quality problems since the quality inspection is frequently finished after a production line. Businesses may benefit from real-time inspection by augmenting robots with vision and AI systems, which helps to cut down on waste and downtime.
Pick and Place
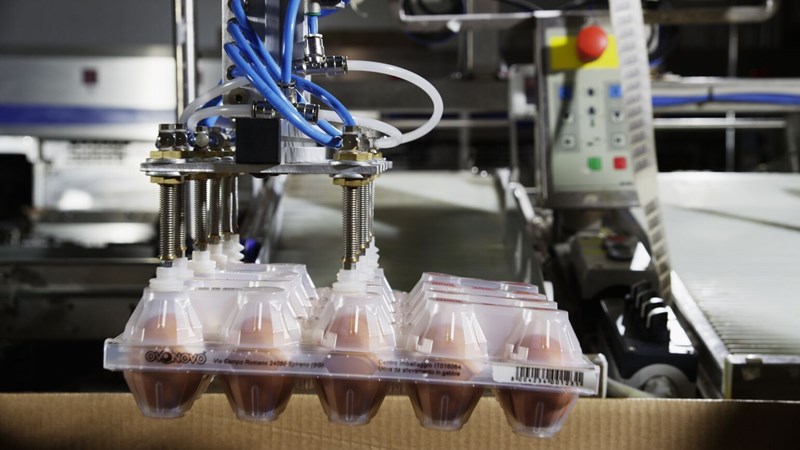
Robots that pick and put items are frequently used in logistics and modern production. To accelerate the manufacturing and distribution of commodities, they are outfitted with cutting-edge machine vision systems that can swiftly and effectively recognize an object, grip it, and transport it from one place to another.
Conclusion
The working of robotic arms is helpful for different industrial and manufacturing purposes that require speed, precision, and repetition. Robotic arms today are used to generate a faster return on investment and improve productivity across multiple industries and sectors. It provides a high degree of accuracy and eliminates humans from doing hazardous tasks. On top of everything else, they have become much more economical and are often sold with different attachments for assigned duties. So, what are you waiting for? Get a robotic arm today to meet your industry targets today.