Di Jim Lawton, Vice President, Product and Applications Management.
Packaging e pallettizzazione includono alcuni dei compiti meno ergonomici nella catena di fornitura, richiedendo agli operatori chiamati in causa un numero significativo di sforzi ripetitivi in grado di causare disturbi muscolo-scheletrici.
Sollevare carichi pesanti e piegarsi per raccogliere o avvolgere merci non sono solo attività non ergonomiche che comportano il rischio di lesioni, ma sono anche ripetitive, il che può portare a errori umani man mano che la capacità di attenzione diminuisce.
Questa combinazione di fattori rende i robot collaborativi un partner ideale per i processi di imballaggio e pallettizzazione.
I cobot UR offrono un ROI fra i più rapidi del settore.
Questo ha generato un elevato interesse da parte delle aziende che cercano modi per gestire i picchi di produzione in maniera flessibile ed economicamente sostenibile. Questa tendenza si è confermata e rafforzata a causa della pandemia COVID-19.
Di fronte a improvvisi picchi di domanda di prodotti come componenti medicali e DPI, diversi clienti hanno adottato con efficacia la nostra tecnologia di confezionamento e pallettizzazione collaborative aumentando produttività e garantendo il rispetto delle norme di sicurezza e distanziamento.
Allo stesso tempo, le restrizioni imposte dal COVID-19, stanno rendendo sempre più ardue le sfide lavorative poste di fronte alle aziende.
La carenza di manodopera e le assenze dovute a malattia o isolamento sanitario, rendono oltremodo difficile far fronte ai picchi di produzione.
Anche l’inserimento di nuovo personale – proprio a causa delle restrizioni imposte dal COVID 19 – è difficoltoso. I cobot possono offrire un contributo prezioso colmando le carenze di manodopera.
I cobot creano posti di lavoro
In alcune situazioni, l'implementazione di cobot su task legati al packaging e alla pallettizzazione, può anche portare a nuove assunzioni di personale grazie ai maggiori livelli di produttività.
Questo è stato il caso di RNB Cosméticos in Spagna. L'azienda ha integrato 6 cobot Universal Robots UR10 nella sua linea di pallettizzazione.
Grazie alle molteplici possibilità di configurazione offerte dalle celle cobot, RNB Cosméticos è stata in grado di aumentare la produzione in modo rapido ed efficiente.
I cobot lavorano collaborativamente con gli operatori su un ciclo di produzione di 6 confezioni al minuto e sono in grado di gestire con flessibilità il fine linea di più di 350 articoli diversi.
L’efficacia del sistema ha comportato un aumento di produttività e l’assunzione di nuovo personale.
Allo stesso tempo, il personale esistente è stato sollevato da compiti non ergonomici e ha aumentato le proprie competenze professionali: invece di imballare e pallettizzare, i lavoratori ora gestiscono le operazioni dei cobot.
“Non stiamo assumendo personale esperto per gestire un robot high-tech. Stiamo trasformando il nostro personale in esperti di robotica incrementando e qualificando le loro competenze ", ha affermato Aurelio Tornero, direttore generale industriale, RNB Cosméticos.
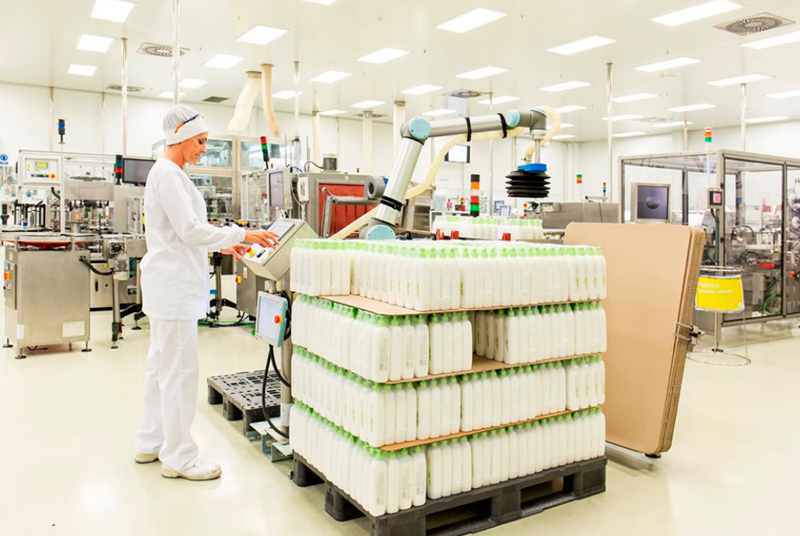
Lo staff RNB - anche se sprovvisto di verticali competenze robotiche - programma facilmente i cobot sulla linea
I cobot migliorano l’ergonomia in L’OrÉal
Nello stabilimento L'Oréal India di Pune, le operazioni di fine linea venivano eseguite manualmente, con operatori che sollevavano circa 8.500 chilogrammi (18.700 libbre) di prodotto per ogni singolo turno di 8 ore.
L'Oréal India ha considerato questo un rischio ergonomico troppo grande per i suoi operatori e ha utilizzato 2 cobot UR10 per sollevare gli operatori da questo compito gravoso.
I cobot hanno migliorato del 5% l'efficacia complessiva delle apparecchiature nello stabilimento, grazie al tempo risparmiato nella composizione dei pallet.
“I robot collaborativi hanno contribuito a eliminare completamente il rischio ergonomico.
Sono facili da usare, esenti da manutenzione ed estremamente efficienti. Siamo davvero felici di avere i cobot di Universal Robots sulla nostra linea ", ha affermato Ranjit Ekda, Head - Manufacturing Supply Chain, L'Oréal India.
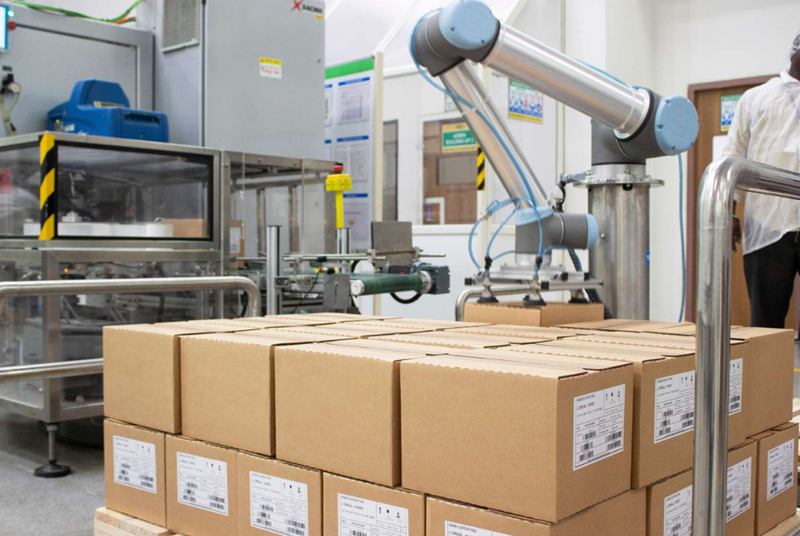
L'Oréal India ha abbutto il rischio ergonomico per i suoi operatori integrando un robot collaborativo nelle operazioni di pallettizzazione.
Sulle linee di packaging di Nippon Zettoc uomini e robot danno il meglio
In Giappone, il principale OEM di dentifrici e prodotti per l’igiene personale, NIPPON ZETTOC CO. LTD., ha introdotto i cobot UR5 per affrontare la carenza di manodopera sulla linea di confezionamento e confezionamento.
"Le persone possono lavorare in modo flessibile, ma ovviamente ci sono punti negativi come il fatto che possono improvvisamente lasciare il lavoro.
Ci sono inoltre profonde differenze nelle competenze", ha affermato Junichi Kano, responsabile del dipartimento di tecnologia di produzione di NIPPON.
"Pertanto, il nostro obiettivo è creare una linea che incorpori le migliori caratteristiche di persone e robot".
La linea di confezionamento dell'azienda dedicata al packagin interno dei prodotti, che prima richiedeva due persone, ora richiede una persona e quattro cobot UR5, consentendo una produzione continua durante le pause dei lavoratori.
Anche gli UR5 hanno accelerato la produzione, fornendo un aumento del 30% del numero di prodotti confezionati all'ora.
La linea di confezionamento della scatola esterna invece è ora completamente automatizzata da un UR5, mentre il personale lavora su attività a più alto valore aggiunto come la fornitura di materiali e l'ispezione del processo.
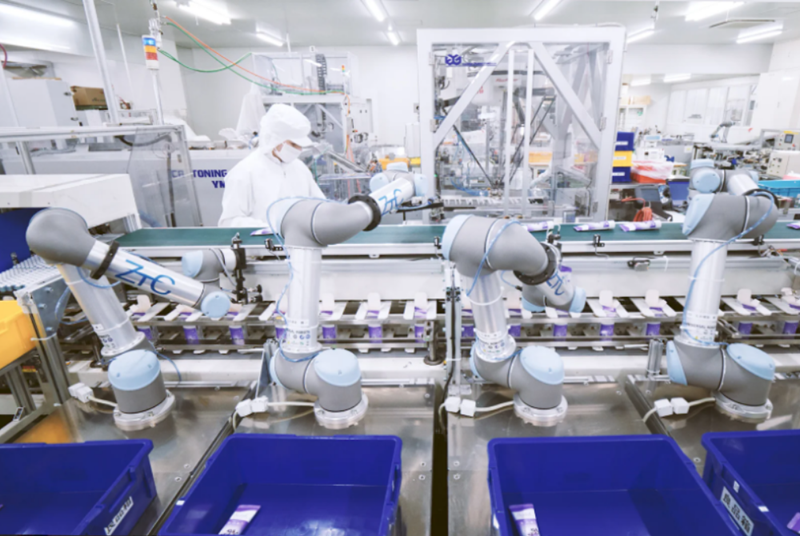
La linea di packaging di NIPPON è sempre attiva e riesce a gestire con semplicità e flessibilità fino a 350 prodotti diversi per forma e dimensione
PALLETTIZZAZIONE, MAI COSì SEMPLICE
La facilità d'uso è una qualità per cui Universal Robots si impegna in tutte le proprie soluzioni.
Per semplificare la programmazione delle attività di pallettizzazione, abbiamo incluso una speciale procedura guidata nel nostro sistema operativo Polyscope.
La procedura guidata consente all'utente di impostare solo gli angoli di una scatola e di aggiungerne le dimensioni, mentre il robot determina dove devono essere posizionate le parti nella griglia.
Tool Gauge, azienda specializzata nella produzione di componenti aerospaziali, ha utilizzato la nostra procedura guidata di pallettizzazione per ridurre i costi di manodopera e liberare i lavoratori da attività ripetitive e dispendiose in termini di tempo presso la sua struttura di Seattle, negli Stati Uniti.
In origine, una parte lavorata in rame, facilmente danneggiabile, veniva prodotta da un macchinista presso una CNC.
Le parti venivano prelevate da uno scivolo, pulite, sciacquarle, asciugate e inscatolate.
Ora, un cobot UR3 raccoglie le parti, le colloca in un bagno di risciacquo, quindi le solleva di fronte a un essiccatore e quindi lascia cadere ogni parte in singole celle di cartone a griglia.
"La procedura guidata di pallettizzazione è diventata la nostra preferita", spiega Steve Ouzsts, ingegnere di produzione di Tool Gauge.
"È così efficiente e facile da programmare." Il direttore generale di Tool Gauge, Jim Lee, stima che la società abbia risparmiato $ 9.000 sin dal primo ordine.
"Non stiamo più sprecando il talento del nostro macchinista, ma possiamo farlo concentrare su progetti di valore più elevato come l'impostazione e la programmazione delle macchine CNC", spiega.
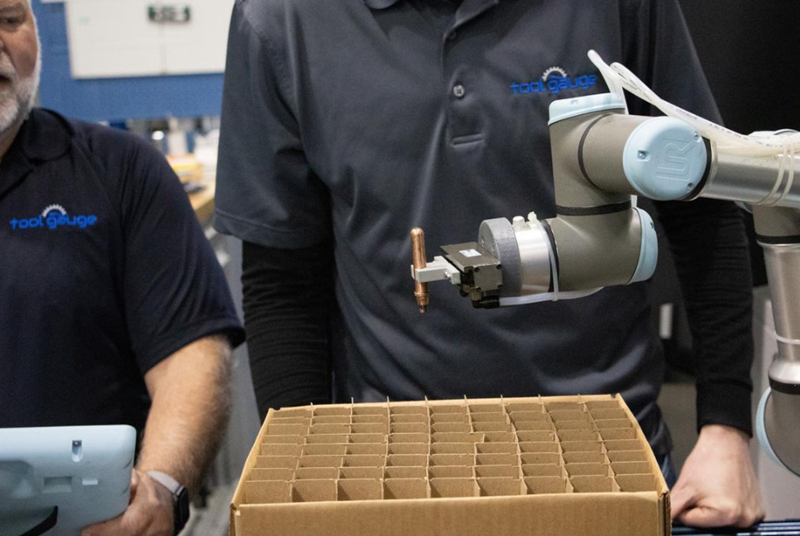
UR3 utilizza la procedura guidata di pallettizzazione incorporata per far cadere con precisione le parti nella griglia della scatola
Ti interessa conoscere i 10 vantaggi che un'azienda può sperimentare applicando un cobot? Scarica e leggi il nostro ebook:

Sei interessato a saperne di più su come Universal Robots aiuta le aziende a combattere COVID-19? Scarica il nostro white paper "Cobots vs Covid".