FLESSIBILI, DELICATI E PRECISI: I COBOT PER I PICK&PLACE AD ALTO VALORE AGGIUNTO nel settore elettronico
In alcuni settori industriali, le lavorazioni devono essere svolte con particolari requisiti come la delicatezza. Infatti, la fragilità e il valore economico dei componenti richiedono l’uso di una tipologia di automazione che sia in grado di applicare un controllo di forza preciso e ben determinato. Ambiti come il medicale, l’aerospace, l’elettronico rappresentano un esempio classico. Il settore elettronico (che fra l’altro fornisce gli altri due) ha a che fare con componenti piccoli e delicati, ma anche piuttosto voluminosi (ad esempio le schede PCB di uso satellitare).
In questo contesto l’automazione che gestisce la movimentazione prima (es. pick and place) e l’assemblaggio dei componenti poi, deve assicurare precisione, ripetibilità di posizionamento, controllo di forza e coppia durante l’assemblaggio.
E sono proprio i cobot impiegati nel settore dell’elettronica di cui andremo a parlare oggi attraverso l’articolazione di tematiche come:
- Il cobot: un soggetto rivoluzionario
- Dubbi e falsi miti
Il cobot: un soggetto rivoluzionario
In un tempo relativamente breve il cobot si è rivelato come soggetto rivoluzionario: un vero e proprio game changer nel settore elettronico perché è stato in grado di assicurare performance di precisione e “delicatezza” più che umane. Anche fattori come dimensioni contenute e collaboratività hanno consentito di mantenere layout aperti (e condivisi) non più segregati da barriere e recinzioni. La condivisione degli spazi è fondamentale per ottimizzare le potenziali prestazioni del cobot e porta i seguenti vantaggi:
- La flessibilità dell’area produttiva è più facilmente convertibile a ogni cambio di processo produttivo.
- Lo spazio può essere condiviso equamente fra operatore e robot e dalla collaborazione viene massimizzato il totale delle prestazioni.
- Le aziende non devono più investire in costosi sistemi di sicurezza come barriere e recinzioni
Universal Robots ha un’ampia offerta di cobot articolata su più taglie, con reach da 500 a 1750 mm e payload incrementali da 3 a 35 kg. Queste caratteristiche consentono di coprire la totalità dei bisogni nelle operazioni di pick and place e nell’assemblaggio puro.
Ora andiamo a fugare alcuni dubbi e sfatare credenze errate che i responsabili di automazione delle industrie elettroniche potrebbero ancora avere riguardo all’implementazione dei cobot all’interno dei processi produttivi.
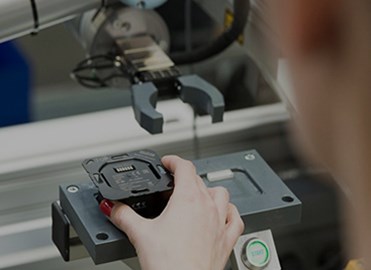
Dubbi e falsi miti
Il settore dell’elettronica è caratterizzato da processi molto serrati, soggetti a mutazioni repentine dovute alla crescente produzione di lotti dai volumi ridotti e personalizzati. Con queste premesse è normale porsi degli interrogativi sul tangibile vantaggio che i cobot possono portare. Fra le domande più comuni:
I cobot possono effettuare l'assemblaggio elettronico a più assi?
Si. Nell'assemblaggio elettronico, la capacità di manipolare una scheda circuito attraverso più assi di movimento è un bisogno comune: questa è una situazione ideale per i cobot a 6 assi. Un cobot può prelevare una scheda dalla linea di assemblaggio e inserirla in un telaio. Ciò comporta spesso l'inserimento di uno dei bordi orientato nel giusto verso, quindi è necessaria la rotazione della scheda nel telaio ma anche l'inserimento con la giusta forza.
Il cobot può anche sistemare il coperchio sul telaio e persino avvitare le viti per chiuderlo: per fare un esempio il modello UR3e è dotato di infinite spin al polso. Vi sono anche tante altre applicazioni pick and place ideali per i cobot, fra le quali:
- La separazione delle schede tra loro.
- L’inserimento ed estrazione delle schede da una staffa di test.
Può un cobot lavorare in collaborazione con un altro cobot in applicazioni come l'assemblaggio a press-fit?
I cobot sono progettati per collaborare con operatori, altri dispositivi automatizzati o altri cobot, quindi la risposta è si. In una linea di assemblaggio, un cobot è ideale per svolgere compiti noiosi, ripetitivi o che possono causare lesioni agli operatori (movimenti ripetuti, posizioni anomale, ecc….). Come abbiamo visto nel paragrafo precedente i cobot possono:
- Separare schede, estrarle o inserirle in posizione
- Avvitare viti, dadi o pressare connettori
Anche l'incollaggio è un ulteriore compito di assemblaggio che può essere facilmente automatizzato poiché il cobot può essere programmato per distribuire l’adesivo in quantità, consistenza e dimensioni precise, anche su geometrie complesse e non regolari. Questo può generare un grande impatto positivo sulla qualità del prodotto.
È anche possibile implementare con facilità una fila di celle robotiche, dove ognuna svolge un compito diverso che termina con la consegna del particolare alla cella di assemblaggio successiva. La flessibilità dei cobot e la loro facilità di programmazione consentono un rapido riutilizzo per svolgere compiti diversi in relazione alle esigenze di produzione del momento. Un altro vantaggio è la possibilità di salvare ogni singolo programma relativo a compiti comuni: in questo modo il tempo di implementazione di ulteriori cobot sarà ridotto al minimo perché sarà sufficiente inserire i programmi esistenti nei “nuovi arrivati”.
È possibile integrare un cobot, un sistema di visione e un EOAT al polso?
Certamente. I cobot UR sono distribuiti esclusivamente attraverso i nostri distributori, molti dei quali possono fornire anche sistemi di visione e attrezzature EOAT oltre ad avere competenze ed esperienza estese nell'industria elettronica. UR ha anche sviluppato un ecosistema unico di periferiche, accessori e software pre-certificati e integrati nel software dei robot.
Scopri lo showroom online UR+ e l'ampia gamma di dispositivi.

I cobot sono sicuri contro i danni da ESD?
Assolutamente si. I cobot UR sono progettati e testati secondo la norma IEC 60001-6-4 per proteggere altre apparecchiature dalle emissioni di scariche elettrostatiche (ESD) del robot. Come buona pratica consigliamo di proteggere le parti manipolate dal robot attraverso l’adozione di misure simili a quelle richieste per gli operatori. Ciò può avvenire attraverso:
- La posa dei cavi di messa a terra collegati allo strumento end-of-arm.
- La considerazione dei materiali e il design dello strumento.
- L’uso di procedure adeguate per garantire che il robot e le parti da manipolare siano allo stesso potenziale elettrico.
I cobot UR sono progettati e testati per soddisfare anche i requisiti della norma IEC 61000-4-2 relativa alla protezione del robot dalle ESD esterne.
Visualizza le specifiche dei robot UR e i manuali nella sezione di supporto del sito web di Universal Robots
Andiamo ora a scoprire alcuni casi di successo. Tre aziende nel settore dell’elettronica che hanno implementato i cobot UR sia per le operazioni di pick and place che per l’assemblaggio:
• KOYO ELECTRONICS INDUSTRIES
• MELECS EWS
• JVC INDONESIA
KOYO ELECTRONICS INDUSTRIES
A fronte dell'aumento nella richiesta di pannelli touch per auto, KOYO ELECTRONICS INDUSTRIES ha dovuto riassegnare i collaboratori dalle attività di ispezione ad altre mansioni con l’obiettivo di risolvere punti critici che rallentavano alcuni processi. Questa scelta ha portato a una carenza di manodopera qualificata nei processi di test dei pannelli touch.
Per questo motivo KOYO ELECTRONICS INDUSTRIES ha iniziato ad automatizzare il processo di ispezione dei pannelli tramite un cobot in grado di gestire diverse forze necessarie al compimento della mansione. La scelta è ricaduta su un cobot UR3 Universal Robots, che offre 3 kg di capacità di carico e 500 mm di raggio operativo, con controllo integrato di forza/coppia e 17 funzioni di sicurezza per una collaborazione sicura uomo-robot. Nel momento in cui l'UR3 tocca un pannello touch senza difetti, appare un "OK" e si accende una luce verde. Se viene rilevato un errore, appare "NG", si attiva una luce rossa insieme a un segnale acustico e viene inviato un avviso al responsabile che può intervenire. Questa iniziale implementazione con l’UR3 ha portato vantaggi come:
• Aumento della produttività del 31%
• Dimezzamento del numero di addetti necessari al processo di ispezione dei pannelli
• Possibilità per gli operatori di svolgere compiti di maggior valore
• Raggiungimento del ROI in soli 12 mesi
MELECS EWS
A seguito di una crescente domanda, MELECS EWS aveva l’esigenza di automatizzare l'imballaggio (inserire link blog Pallettizzazione) di piccoli circuiti stampati. Grazie alla nota praticità dei cobot UR, MELECS EWS ha scelto un cobot UR5 da implementare nel processo di pick and place relativo all'imballaggio. L’operatore posiziona circuiti stampati nell'area di lavoro dell'UR5 il quale provvede a scansionare, prelevare tre schede e posizionarle su di un vassoio. Una volta riempito il vassoio il cobot provvede alla sua chiusura. L’UR5 ha consentito a MELECS EWS di:
• Imballare due milioni di componenti senza alcun errore
• Aumentare del 25% la produttività del processo di imballaggio
• Eliminare i punti critici e i colli di bottiglia nel flusso produttivo
JVC ELECTRONICS INDONESIA
L’esigenza di aumento della produttività e la garanzia di una qualità costante ha spinto JVC ELECTRONICS INDONESIA ad automatizzare il processo di avvitatura. L’implementazione di ben sette cobot UR3 ha consentito di gestire le attività ripetitive nella fase di assemblaggio e di assolvere con successo al processo di avvitatura. I cobot UR hanno permesso a JVC ELECTRONICS INDONESIA:
• Il miglioramento dei processi
• La garanzia di maggiore sicurezza per gli operatori
• Una riduzione dei costi operativi pari a oltre 80.000 $
• Lo svolgimento di compiti di maggior valore da parte degli operatori
Questi tre casi di successo nel settore elettronico dimostrano come i cobot siano in grado di integrarsi facilmente nei processi produttivi dove movimentazione e pick and place sono operazioni comuni. I cobot UR operano in completa sicurezza a fianco dei colleghi umani e non necessitano di recinzioni o aree delimitate poiché possono occupare uno spazio molto ridotto.
Vuoi saperne di più?
Compila il form qui sotto e scarica il nostro eBook dedicato all'industria elettronica!