Principali vantaggi dei Cobot per le aziende
Ecco i vantaggi che le aziende possono sperimentare applicando i robot collaborativi ai propri processi (leggi questo articolo se vuoi approfondire alcuni vantaggi dei robot collaborativi: Il futuro è collaborativo. i vantaggi dei cobot nei processi di automazione). Si tratta di esempi concreti di imprese che hanno integrato i cobot Universal Robots.
Produttività
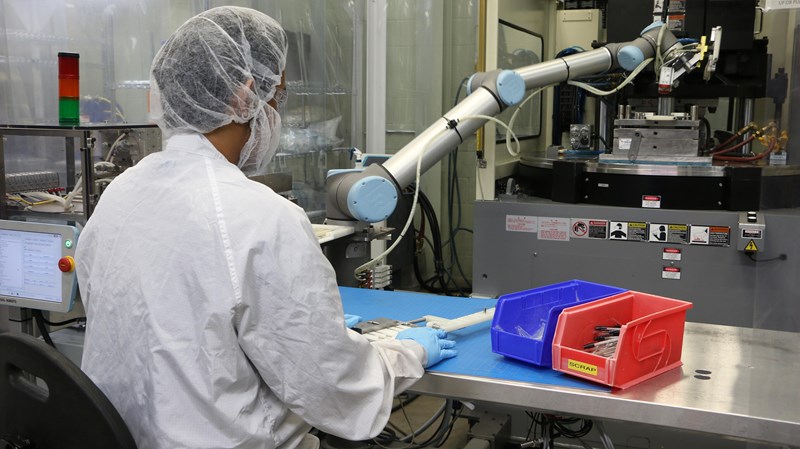
Dynamic ha trovato nei cobot Universal Robots lo strumento perfetto per aumentare la produttività. La natura dei materiali in lavorazione nel settore plastico non ammette deroghe: il rispetto dei tempi di lavorazione è fondamentale trattandosi di materiali termosensibili.
Grazie ai cobot applicati nelle varie fasi dello stampaggio, nel kitting e nella pallettizzazione degli stampati, Dynamic ha quadruplicato la propria produzione incrementando anche la qualità dei prodotti.
La semplicità di integrazione ha fatto che sì che le 3 celle fossero operative in appena 2 giorni. Dynamic sta progettando l’automazione di altre attività con i cobot, una possibilità offerta dalla loro elevata flessibilità operativa.
Guarda il video sulla testimonianza di Dynamic sull'utilizzo dei robot collaborativi.
Qualità
Nella sua ricerca di una produzione sempre più snella e smart, RUPES si è impegnata per raggiungere l’obiettivo “zero difetti” nei suoi prodotti e ha contattato Universal Robots per una soluzione di automazione che supportasse la sua eccellente forza lavoro, minimizzasse gli sprechi e portasse risultati immediati.
RUPES ha impiegato i robot collaborativi UR nella sua linea di produzione affinché assumessero i compiti più pesanti e ripetitivi e liberassero il personale perchè potesse dedicarsi a compiti più gratificanti.
I robot UR sono stati infine in grado di risolvere facilmente la sfida di automazione più ardua che sperimentava Rupes:il serraggio dei componenti delle apparecchiature in fase di assemblaggio. Il posizionamento preciso e la funzione di regolazione della potenza inclusi in UR3, hanno assicurato che ogni vite fosse fissata secondo le specifiche esatte.
Guarda il video sulla testimonianza di Rupes sull'utilizzo dei robot collaborativi.
Gestione della forza lavoro
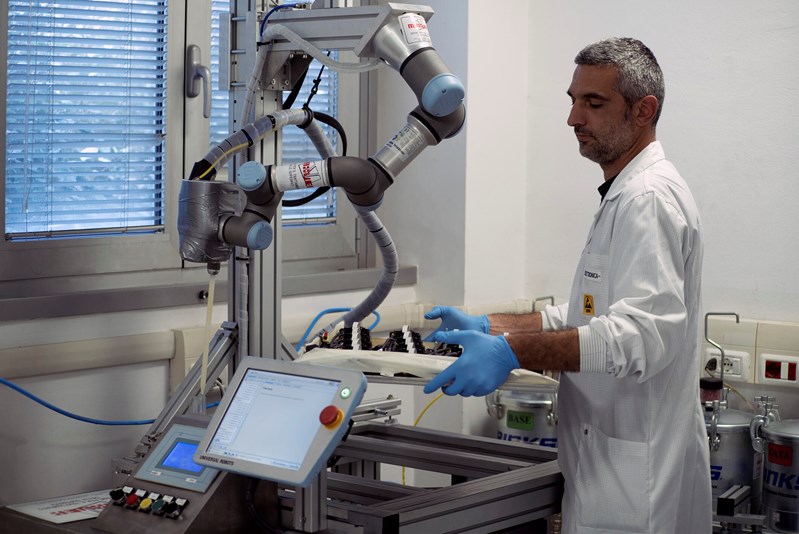
Life Elettronica è tra le aziende italiane leader nella produzione conto terzi di schede elettroniche. L’azienda esegue tutte le lavorazioni presso il proprio stabilimento di Modena, dalla presa in carico del progetto alla consegna del prodotto finito.
Life Elettronica ha scelto di automatizzare una fase di processo – la resinatura - sostituendo la macchina precedentemente in uso che necessitava della presenza costante di un operatore, con un robot collaborativo. Il cobot opera in un’area di lavoro ristretta ed è in grado di resinare 16 schede elettroniche contemporaneamente. Il ciclo di lavoro complessivo, della durata di 15 minuti circa, non ha paragoni con le classiche metodologie di resinatura, svolte con l’ausilio di altri macchinari e, soprattutto, con la presenza costante dell’operatore a vigilare sul processo. Life è così riuscita a incrementare esponenzialmente la propria produttività sollevando l'operatore precedentemente dedicato alla fase per impiegarlo su task a maggior valore aggiunto.
Guarda il video sulla testimonianza di Life Elettronica sull'utilizzo dei robot collaborativi.
Refitting
All Axis Machining, per molto tempo ha cercato, senza esito, una soluzione per automatizzare le sue vecchie CNC e mantenerle in funzione anche durante i turni ciechi.
Dopo aver visto in azione i piccoli, ma efficienti robot collaborativi, si è convinta di aver di fronte la giusta soluzione per automatizzare i propri processi, pur continuando ad utilizzare le sue “attempate” macchine a controllo numerico. Infatti, grazie alla piattaforma Universal Robots +, lo store online che raccoglie oltre 250 soluzioni plug&play certificate all’uso con i cobot UR, e al software development kit, All Axis è stata in grado di trovare la giusta soluzione per integrare il cobot UR10 alle sue macchine. Il vantaggio sperimentato dall'azienda americana è stata una maggiore produttività - pur mantenendo in opera le sue vecchie apparecchiature - e una migliore gestione dei turni e della forza lavoro.
Guarda il video sulla testimonianza di All Axis Machining sull'utilizzo dei robot collaborativi.
Se vuoi saperne di più sui cobot e conoscere tutti i vantaggi che possono darti, scarica il nostro ebook:

Flessibilità nei cambi di produzione
La giapponese Nippon Zettoc, prima di introdurre 5 robot collaborativi Universal Robots nelle sue linee produttive, ha sperimentato una serie di difficoltà: non riusciva ad automatizzare i suoi processi con la necessaria flessibilità.
In particolare la gestione di diversi prodotti sulla stessa linea logistica è stata affrontata sfruttando al massimo la possibilità plug and play offerta dai cobot UR: la sostituzione dell’end effector installato e il lancio di programmi preimpostati, permette all’azienda di gestire i cambi produttivi in pochi minuti, facendo fronte, in tempi rapidissimi, al packaging degli oltre 350 articoli della sua gamma. Un esempio della grande flessibilità di cui sono dotati i cobot Universal Robots.
Guarda il video sulla testimonianza di Nippon Zettoc sull'utilizzo dei robot collaborativi.
Gestione dei picchi di lavoro
RSS è una piccola azienda californiana di meno di 80 dipendenti che opera nel settore del mobile e delle attrezzature specializzata nella produzione di rubinetterie. In difficoltà per l’evasione di un grosso ordine (700 rubinetti in un mese) ha deciso di esplorare il mondo della robotica collaborativa. Le sue macchine CNC erano in grado di produrre 400 rubinetti per mese lavorando su due turni giornalieri, quindi anche aggiungendo un terzo turno alla produzione non sarebbe stata in grado di rispettare la commessa. Con l’introduzione del cobot UR5, in asservimento alla CNC (scopri di più sull'applicazione di asservimento alla CNC con i robot collaborativi), è riuscita invece a produrre tutti i pezzi ordinati in soli 11 giorni. L’implementazione del cobot nelle linee produttive di RSS ha prodotto un incremento di produttività complessivo di oltre il 30%.
Guarda il video sulla testimonianza di RSS sull'utilizzo dei robot collaborativi.
Gestione del layout
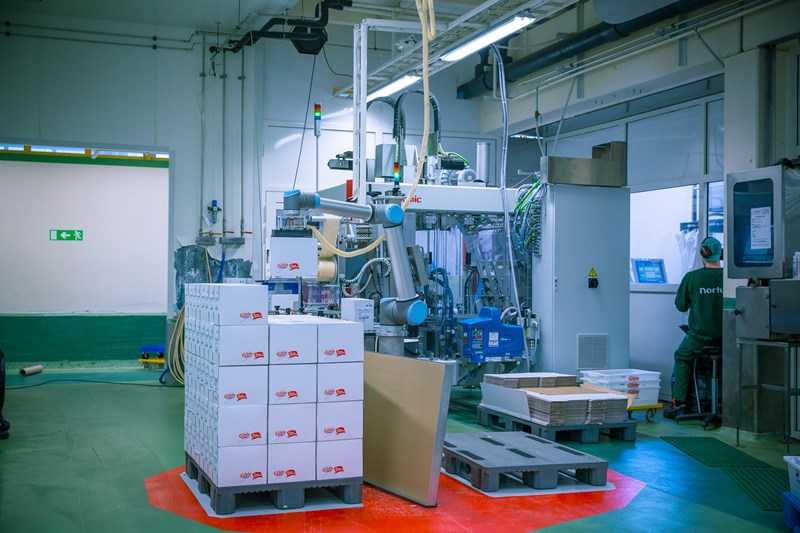
Nortura è un’azienda norvegese attiva nel settore alimentare e specializzata nella produzione di carni. Le sue esigenze, legate al processo di pallettizzazione (scopri come funziona la pallettizzazione con i robot collaborativi), erano essenzialmente due:
- Predisporre un processo che operasse con continuità senza interrompere la linea di produzione
- Rendere lo spazio occupato dall’applicazione fruibile quando questa non era attiva, gestendo il layout in maniera efficace e flessibile.
I cobot hanno fornito una risposta a queste due esigenze. Nortura ha installato un braccio robotico UR10 su un lift e un sistema di visione a soffitto. L’area di pallettizzazione è stata tracciata sul pavimento: un semplice rettangolo di vernice. Quando l’operatore sistema nel rettangolo un pallet vuoto, il sistema di visione lo riconosce e attiva il cobot che inizia a pallettizzare i colli in pedana secondo il pattern impostato. In assenza di pallet nel rettangolo il braccio staziona in posizione di riposo e lo spazio a pavimento rimane disponibile per ogni altra attività. Nortura ha risparmiato circa il 90%dello spazio che usualmente è necessario per sviluppare un’applicazione di pallettizing.
Guarda il video sulla testimonianza di Nortura sull'utilizzo dei robot collaborativi.
Ridurre lo skill gaP
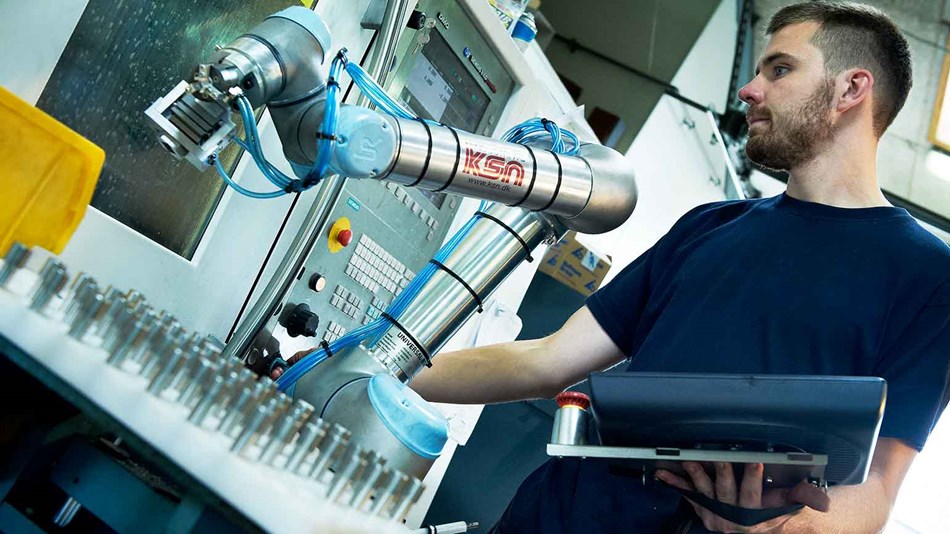
Quando la giovane azienda danese Nymann Teknik, specializzata in lavorazioni meccaniche con macchine utensili, ha ricevuto un ordine di 100.000 unità, ha compreso che era necessario automatizzare l’asservimento del proprio tornio CNC. Universal Robots ha fornito la risposta alle esigenze di Nymann. Oggi UR5, il modello intermedio prodotto da UR (5kg di payload, 850 mm di sbraccio per meno di 19 kg di peso) alimenta un tornio CNC con materiali in acciaio, lavorando fianco a fianco con il personale senza barriere di sicurezza. Introdurre il nuovo "collega" nell'azienda si è rivelato un compito di una semplicità disarmante, gestito dagli operatori di Nymann senza l’intervento di tecnici esterni. Oggi gli addetti alla produzione hanno acquisito una competenza specifica nella programmazione del cobot UR e possono gestire parti del processo a più alto valore aggiunto, venendo sollevati dalla ripetitiva attività di caricamento della macchina.
Guarda il video sulla testimonianza di Nymann Teknik sull'utilizzo dei robot collaborativi.
Aumentare Ergonomia e sicurezza
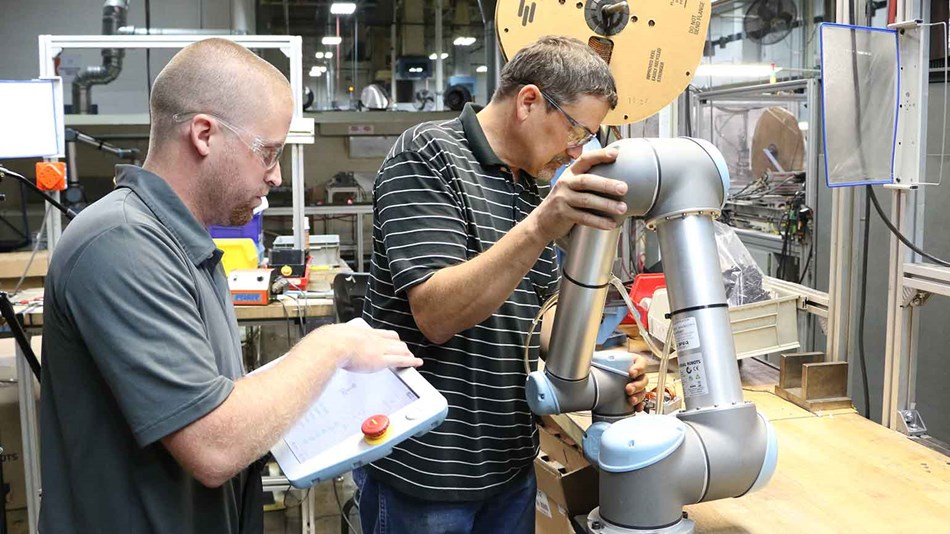
SCOTT FETZER ELECTRICAL GROUP, azienda statunitense del settore elettronico, ha integrato 2 cobot UR nelle operazioni connesse alla lavorazioni di lastre metalliche e cavi, applicando i cobot in operazioni ripetitive e usuranti come il taglio dei cavi stessi con taglierine, attività che esponeva gli addetti a un serio rischio di sviluppare la sindrome del tunnel carpale. L’integrazione dei cobot UR nelle attività produttive le rende, non solo più efficienti, ma anche più sicure per gli addetti.
Guarda il video sulla testimonianza di SCOTT FETZER ELECTRICAL GROUP sull'utilizzo dei robot collaborativi.
Roi Elevato
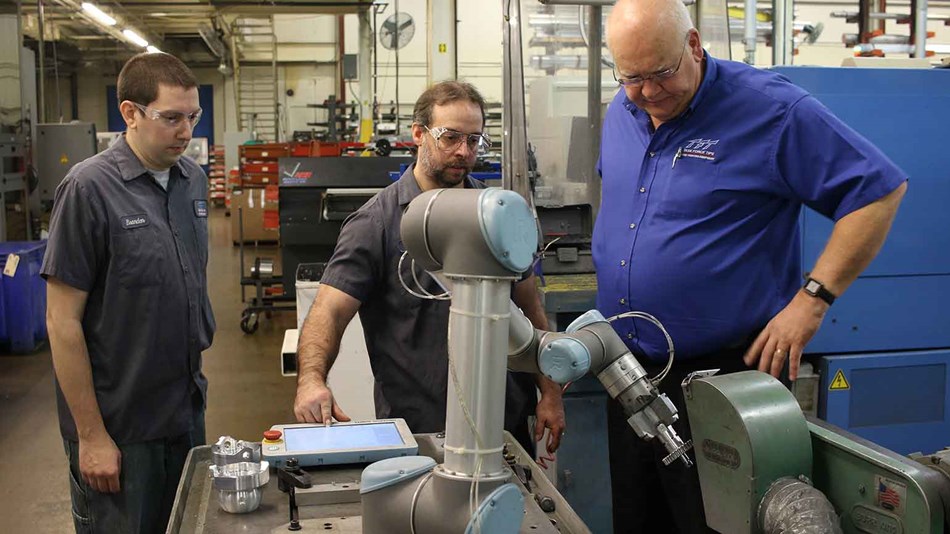
Task Force Tips ha installato un robot UR10 e due UR5 che si occupano dell'asservimento delle macchine CNC, mentre un quarto UR5 è stato montato su una base mobile su ruote e viene spostato tra le diverse attività. Un elemento che in precedenza impediva di utilizzare i robot erano le barriere di sicurezza necessarie attorno alla macchina. L’enorme vantaggio rappresentato dalla robotica collaborativa UR è che non sono necessarie protezioni e i cobot possono essere dislocati e installati esattamente dove occorre all'interno del processo produttivo.
Anche il fatto che i due robot UR5 lavorino in coppia ha aiutato a ottimizzare la produzione. Quando arrivano i pezzi grezzi da un trasportatore in ingresso, il primo robot UR5 utilizza la guida visiva per identificare e afferrare i pezzi e quindi li inserisce nella prima fresatrice. L’UR5 estrae quindi la parte semilavorata già nel tornio e la passa all’altro UR5. Il secondo robot inserisce la parte nella seconda macchina, estrae il pezzo finito e lo posiziona su un trasportatore in uscita, dove un operatore posiziona i pezzi sulle griglie di anodizzazione, completando il ciclo.
Il fatto che il personale venga liberato dall’obbligo di occuparsi delle macchine, ha svolto un ruolo molto importante nell’aumento della qualità dei prodotti.
Ora infatti possono essere dedicati ad attività a più alto valore aggiunto quali il controllo qualità e le ispezioni sui prodotti lavorati, consentendo di innalzare notevolmente la qualità dei prodotti Task Force Tips.
Guarda il video sulla testimonianza di Task Force Tips sull'utilizzo dei robot collaborativi.