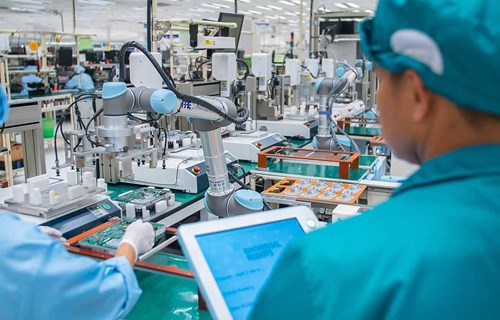
ユニバーサルロボットの協働ロボットは、世界中の電子機器メーカーで採用され成功のカギとなっています。用途はそれぞれ異なりますが、全体でみるとどれも明らかな成果が出ています。その成果とは、生産性と品質の向上、反復作業のヒューマンエラー減少、職場環境の改善です。
今週のブログでは、想定外の需要急増・熟練人材の不足・多品種少量生産・製造施設のスペース不足といった大きなビジネス課題を抱えた電子機器メーカーで、URの協働ロボットが強い味方になった例を紹介します。
光洋電子工業株式会社(以下、光洋)は、製造している車載用タッチパネルの需要急増に対処する必要がありました。光洋は手動で最終検査を行っていた作業員を別のボトルネック工程に配置して対応しましたが、その結果ライン最終工程でタッチパネル検査を繰り返す熟練人材が不足してしまいました。
光洋は、さまざまな強度でタッチパネル検査ができ、人間の隣でも安全柵なしで使え、コンパクトで既存のラインを大きく変えずにすむ自動化技術を必要としていました。そして選んだのがユニバーサルロボットの協働ロボットUR3でした。UR3は強度調節モードを備え、人とロボットの協働を前提に設計された安全機能も数多く搭載しながら省スペースです。
生産性が31%アップ
その成果は目ざましく、UR3を導入して光洋の生産性は31%向上しました。タッチパネルの検査工程に要する人員は2人から1人と半減し、作業員は協働ロボットのオペレーションをはじめとする、体に負担の少ない高付加価値の作業に注力できるようになりました。投資回収期間はわずか12ヶ月でした。
UR3がタッチパネルにスタイラスを当てて何も異常がなければ表示機に「OK」のメッセージが表示され、シグナルタワーの緑のライトが点灯します。異常を感知すると「NG」と表示されシグナルタワーの赤いライトが点灯し、連続でブザーが鳴ります。これにより担当者はすぐに異常に気づき、対応できるようになっています。
Melecs EWS社(以下、Melecs)は製品への需要急拡大に直面し、これに応えるため同社の小型のプリント基板ラインの最終工程である梱包の自動化を目指しました。梱包は手動の3シフト制で、モジュールあたり5〜6秒で終わらせる必要のある単調な作業でした。UR協働ロボットの価格の手頃さと使いやすさが決め手となってMelecsは協働ロボットUR5を1台導入し、こうした体に負担のかかる作業はロボットが受け持つようになりました。
部品200万個も正確に梱包。短いサイクルタイムを実現
その結果、Melecsは梱包工程のスループット25%アップを達成。ボトルネックを解消し、体に負担が大きく時間のかかる作業から作業員を解放しました。短いサイクルタイムが求められるなかでも、協働ロボットは年間約200万個の部品をエラーなく梱包します。
作業員が複数のプリント基板をUR5 の作業エリアに配置するとUR5がレーザースキャナで基板3枚をスキャンします。UR5に搭載されているカスタマイズされた3つのフローグリッパが基板を1枚ずつ持ち上げ、3枚の基板を同時にトレーに配置します。そして、トレーがいっぱいになるとバキュームグリッパで箱に入れ、箱がいっぱいになったらフタを閉じます。
JVC Electronics Indonesia社 (以下、JEIN)は、生産性拡大と品質安定化、さらに厳しい納期といった課題を抱えていました。そこで、手動で時間がかかっていたネジ止め工程の自動化を決めました。
JEIN はさまざまな工程に対応したエンドエフェクタを搭載できるUR協働ロボットの汎用性の高さに注目しました。最終的に同社は電子機器製造ラインのネジ止め、ハンダづけ、ピック&プレイス工程などのために協働ロボットUR3を7台導入しました。
作業員の安全性が向上し、運用コストは削減
その結果、JEINは製造工程の改善と安全性の向上に成功。さらに年間運用コストを8万米ドル以上削減できました。
JEINでは、切断されたプリント基板を分けたりカーステレオユニットにガラス製の画面を取り付けたりといった、体に負担のかかる反復作業に協働ロボットを使っています。こうした工程から解放された作業員はより付加価値の高い作業に取り組めます。さらに、均質性も向上し、一工程あたりの作業時間も半分に短縮できました。
電子機器製造での協働ロボット導入についてはURエキスパートにお問い合わせください