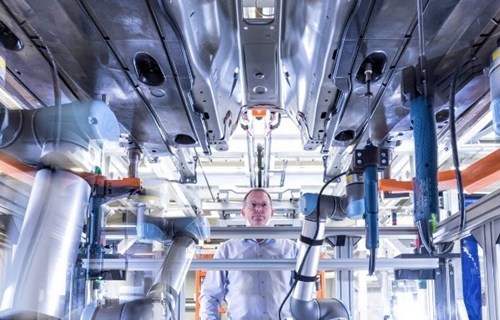
전기 자동차의 선구자 엘론 머스크가 자동차 생산 공정에서 ‘인간은 과소평가된다’라고 트윗을 올렸을 때, 이 말에는 유니버설 로봇 철학의 핵심 원칙이 반영되어 있습니다. 즉, 인간과 로봇의 협동은 로봇이나 인간이 혼자 일하는 것보다 더 나은 결과를 얻을 수 있다는 것입니다. 인간-로봇 협업의 영향을 조사한 MIT 연구에서도 똑같은 결론에 도달했으며, 협동로봇과 함께 작업할 때 작업자의 유휴 시간이 85% 감소한 것으로 나타났습니다.
자동차 산업은 전통적인 산업용 로봇을 가장 먼저 채택한 업종이자 코봇을 가장 널리 적용한 업종 중 하나였습니다. 오늘날은 Tier 1 및 2 공급업체의 부품과 하위 어셈블리 생산에서부터 OEM 생산 라인에서 출하되는 최종 제품에 이르기까지 자동차 제조의 거의 모든 측면에 자동화가 적용됩니다.
자동차 제조사와 자동화의 관계는 수십 년 동안 진행되어 왔지만, 2019년 국제로봇연맹(International Federation of Robotics)에 따르면 기존 산업용 로봇에 비해 코봇은 더 크게 성장했습니다. 그렇다면, 자동차 생산의 어떤 문제점이 코봇 수요의 성장을 이끄는 것일까요?
유니버설 로봇의 자동차 전문가가 설명하는 이번 블로그 글에서는 UR 코봇이 해결하는 자동차 생산의 몇 가지 문제점과 자동화에서 점점 중요해지는 협동로봇의 유연성을 살펴보고, 자동차 부문의 요구에 직접 대응하여 개발된 몇 가지 UR 솔루션을 보여 드립니다.
시동을 걸 준비가 되셨습니까? 그럼 시작하겠습니다.
유니버설 로봇의 코봇은 유연성, 작은 설치 면적, 빠른 ROI, 일관된 성능으로 자동차 생산 부문에서 그 견인력이 점점 커지고 있습니다.
문제점 제거
자동차 제조는 수십 년 동안 부분적으로 고도의 자동화가 이루어졌습니다. 그러나, 특히 조립 작업 등의 일부는 ‘수작업에 크게 의존’하는 상태라고 UR 소프트웨어 제품 관리자 Jacob Bom Madsen은 말합니다. UR 코봇의 유연성과 작은 설치 면적이 실제로 자동차 제조업체에 도움을 주고 있는 곳은 나사 조립과 같은 작업입니다. Bom Madsen은 “대다수의 자동차 생산 시설은 100,000평방미터나 되는 확장 부지를 찾을 수 없는 도시 지역에 있습니다”라며, “코봇의 훌륭한 장점 중 하나는 유연성입니다. 어떤 방향으로든 장착할 수 있고, 위험성 평가를 거친 후에는 안전 울타리 없이 인간 옆에 배치하여 다양한 작업을 성공적으로 수행할 수 있습니다. 결정적으로 도시 지역 자동차 제조업체의 경우, 코봇은 설치 면적이 작기 때문에 기존 생산 라인에 쉽게 추가하거나 받침대에 장착하거나 이동 플랫폼에 장착할 수도 있습니다.”라고 말합니다.
예를 들어 거대 자동차 회사 Opel은 독일 Eisenach의 최신 제조 시설에 UR10 코봇을 배치하여, 작업자는 엔진 블록의 에어컨 압축기에 나사를 조립하는 비인체공학적 작업을 직접 할 필요가 없습니다. UR 글로벌 제품 관리자 Frank Croghan은 “이는 사람이 근무조별로 하루 8시간씩 할 작업이 아닙니다”라면서, “코봇은 작업자의 건강과 안전을 개선하는 동시에 일관된 나사 조립 성능을 보장합니다.”라고 설명합니다.
한편, 유럽에서 두 번째로 큰 자동차 회사 PSA 그룹은 Sochaux의 대규모 공장에 UR10 코봇을 배치하여 차체 조립 라인의 나사 조립 작업을 처리하고 있습니다. 그 결과 기하 공차(geometric tolerance)가 개선되고 작업자의 인체공학적 작업 조건이 향상되었으며 생산 비용이 절감되었습니다.
자동차 제조와 같이 규제가 엄격하여 추적성이 중요한 부문에서는, 차체의 나사 조립에 적용되는 토크 정밀도 등 주요 생산 공정 제어와 추적에 있어서도 코봇이 유용하다고 UR 글로벌 핵심 고객 관리자 Sebastian Lars Lange는 전합니다. 그는 UR 코봇의 매력은 나사 조립 작업에 그치지 않는다고 덧붙입니다. “UR 코봇은 자동차 부문에 사용되어 품질 검사, 소형 부품 조립, 부품 공급, 마감 작업 등을 수행하고 있습니다. 우리의 목표는 자동차 산업이 Tier 1 및 Tier 2 공급업체에서 OEM에 이르기까지 제조 공정의 모든 부분에 로봇을 배치 가능하도록 하는 것입니다.“
자동차 회사를 위한 새로운 UR 제품
이렇게 높은 유연성을 달성하기 위해 유니버설 로봇은 최종 사용자의 의견에 귀를 기울이고 그에 따라 제품을 개선한다고 Bom Madsen은 설명합니다. “예를 들어 UR의 e-시리즈 플랫폼에 사용하는 새 케이블 세트는 e-시리즈 로봇을 자동차 제조 라인에 쉽게 통합할 수 있도록 유연성을 높여 달라는 자동차 제조업체의 요청을 검토한 결과 개발되었습니다." 이제 UR의 최신 케이블 세트 제품은 기본 플랜지 커넥터와 함께 제공됩니다. 이 커넥터는 로봇 베이스에 있는 하나의 플러그로, 훨씬 더 유연하게 코봇을 배치하고 수리할 수 있도록 설계 되어 있습니다. Bom Madsen은 “제조 라인에 로봇이 있으면 두 가지 문제가 발생할 수 있습니다.”라면서, “로봇이 고장나거나 로봇 케이블이 끊어지는 것입니다.” 새로운 베이스 플랜지 커넥터를 사용하면 로봇 고장이 발생했을 경우 케이블과 설치물을 그대로 둔 채 로봇만 떼어내고 새 로봇을 같은 자리에 놓은 다음 케이블을 다시 연결할 수 있습니다. 북미 자동차 회사인 한 고객은 이 공정을 포뮬러 원 경기에서나 볼 수 있는 아주 빠른 타이어 교체에 비유합니다.”라고 전합니다.
대부분의 자동차 생산 라인 자체와 그 주변의 공간은 협소하기 때문에, 제조업체는 로봇 자산을 생산 라인에 가까이 두고 제어 캐비닛은 따로 ‘캐비닛 아일랜드’로 옮기는 것을 좋아한다고 Bom Madsen은 설명합니다. “공간이 협소하다 보면 실제 운영에 필요한 것들만 두려고 합니다. 제어기는 실제로 공정 작업을 수행하지는 않기 때문에, 고객은 차체 가까이에는 운전자와 기타 장비를 위한 공간을 확보할 수 있도록 더 긴 케이블을 제공해 달라고 요청했습니다.“ 그 결과 새로운 e-시리즈용 케이블 세트에는 코봇 배치 시 유연성이 훨씬 높아지는 12미터 옵션이 새로 포함되었습니다.
마찬가지로, 자동차 제조업체는 천장 및 갠트리 장착 및 제7차 축 레일 설정으로 코봇의 작동 영역을 확장할 방법을 찾고 있었습니다. 이를 위해 UR은 e-시리즈용 케이블 세트에 새로운 하이플렉스(high-flex) 케이블 옵션을 제공하여 해당 배치를 지원했습니다. Bom Madsen은 “하이플렉스 케이블은 특정 굴곡 반경에서 5백만회의 반복된 구부림을 견딜 수 있도록 설계되었습니다."라고 설명합니다. “이는 효과적인 제7차 축 설치를 지원하여 코봇의 작동 영역을 크게 확장할 수 있습니다.”
자동차 회사는 또한 3PE(3-postion enabling) 장치가 통합된 새로운 e-시리즈 티치 펜던트의 개발에 동인을 제공했다고 Croghan은 밝힙니다. “유럽의 몇몇 주요 자동차 제조업체들이 일부 애플리케이션에서 e-시리즈 티치 펜던트와 3PE 장치를 완전히 통합하는 것이 유용하다는 것을 발견했습니다. 그래서 우리는 이 제품을 기계적으로나 소프트웨어 측면에서 그대로 완전히 통합하였습니다. 따라서 매우 직관적이며 UR 코봇에 대한 교육을 받은 사람이라면 누구나 매우 쉽게 사용할 수 있습니다.”
새로운 e-시리즈 티치 펜던트와 케이블 세트 등의 제품 개발은 유니버설 로봇의 전체 품질 약속의 매우 중요한 부분이라고 Croghan은 덧붙입니다. “우리는 고객의 요구를 바탕으로 시작했고, 이러한 요구를 충족하는 제품을 만드는 작업을 철저히 이행했습니다. 그리고 모든 제품은 아주 엄격한 테스트를 거치고 있습니다.”
자동차 부문의 Tier 1 및 2 공급업체 또는 OEM이라면 누구나 유니버설 로봇의 유연한 코봇을 사용해 생산량을 늘리고 공정을 간소화하며 품질을 개선할 수 있습니다. 지금 유니버설 로봇의 자동차 애플리케이션 전문가와 상담하여 자세히 알아 보십시오!