Endüstriyel fabrika otomasyonu alanında, genellikle risk değerlendirme sürecinin zaman alıcı, karmaşık ve zorlayıcı olduğuna dair yaygın bir algı mevcuttur. Bu algının temelinde, mühendislerin genellikle net kararları tercih etmeleri ve risk değerlendirmesinin ise bir dizi karar almayı gerektirmesi yatar. Çoğu durumda, risk değerlendirmesine başlamadan önce sürecin yapılarını, standartlarını, adlandırma ve numaralandırma sistemlerini öğrenmek zor gelebilir. Ayrıca, çoğu mühendis için risk değerlendirmesine nasıl başlanacağı veya gerekli eğitim kaynaklarının nereden bulunabileceği gibi karmaşık konular da bulunmaktadır.
KONULARI VE GEREKSİNİMLERİ BELİRLEYİN
Universal Robots, risk değerlendirme hizmetleri sunmamakla birlikte, kullanıcıların risk değerlendirme süreçleriyle ilgili ihtiyaçlarını anlamalarına yardımcı olmak için üçüncü taraf hizmet sağlayıcılarıyla iş birliği yapmaktadır. UR, UR Akademi Risk Değerlendirme Modülleri'ni normal müfredatının bir parçası olarak sunarak bu alanda kullanıcılara destek sağlamaktadır. Ayrıca, birçok sistem entegratörü artık standart projelerinin bir parçası olarak risk değerlendirme hizmeti veriyor.
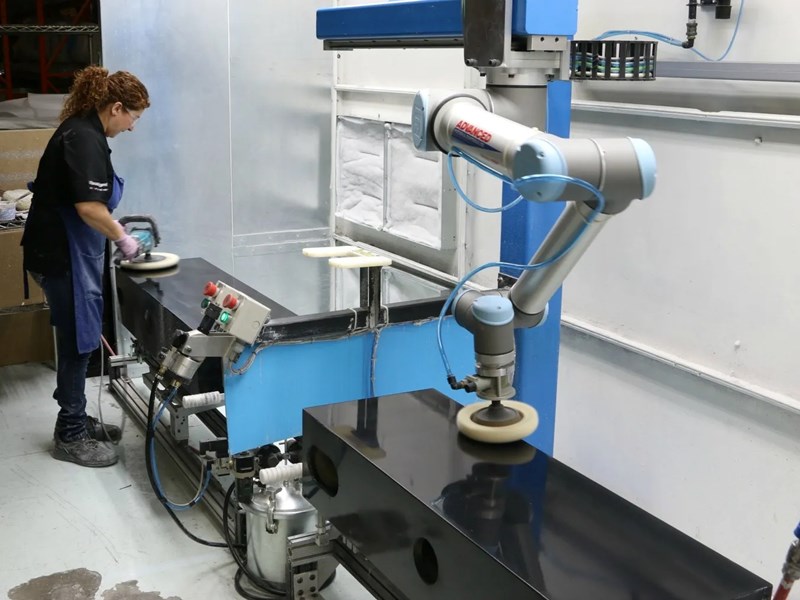
ULUSLARARASI GÜVENLİK STANDARTLARI
ISO 10218-2 ve ISO 102:2011 uluslararası güvenlik standartlarını ifade eder. Bunların 2024'te yayınlanacak revizyonları olacak.
ANSI R15.06-2012, ABD'nin her iki ISO standardını da hiçbir değişiklik olmaksızın benimsemesidir. Yeni revizyon aynı zamanda R15.06'nın 2023 versiyonunun yerini alarak ABD'nin benimsediği bir versiyon haline gelecektir.
Revizyonlar ISO/TS 15066, ISO/TR 20218-1, ISO/TR 20218-2 ve RIA TR R15.806'yı içermektedir.
ANSI VE ISO ROBOTİK STANDARTLArı 2 bölümden oluşur:
1) Manipülatör ve el kumandası olan veya olmayan kontrol ünitesinden oluşan robot: Bu, robot üreticisinin sorumluluğundadır.
2) Entegrasyon, uç efektörler, uygulama, koruma ve ilgili ekipmanı içeren robot uygulaması ve hücresi. Bu, uygulamayı veya hücreyi tasarlayan, bir araya getiren ve entegre eden şirketin sorumluluğundadır. Son kullanıcı, uygulamayı veya hücreyi tasarlıyorsa entegratör de olabilir.
A3 (Otomasyonu Geliştirme Derneği), ANSI standartlarını ve teknik raporları yönetir. A3, robot bilimi alanında ABD'yi ISO'da temsil etmek üzere ANSI tarafından belirlenen kuruluştur.
Endüstriyel robot teknolojisine yönelik ana standartlara (ISO 10218-1 ve ISO 10218-2) ek olan bir ISO Teknik Şartnamesi 15066 ve birkaç ISO Teknik Raporu bulunmaktadır.
OSHA'da herhangi bir robot düzenlemesi yoktur, çünkü endüstri aktif olarak güvenliğin peşindedir. OSHA 4. bölümün robotiğe odaklandığı bir teknik kılavuzu (OTM) vardır. Bölüm 4, yakın zamanda NIOSH/OSHA/A3 Alliance'ın bir parçası olarak UR'nin katılımıyla güncellendi.
Karmaşıklığı biraz basitleştirdiğimizde ISO/TS 15066 (RIA TR R15.606) ile karşılaşıyoruz; burada 100 yetişkinle yapılan bir çalışma, vücutlarının çeşitli kısımlarında yarı statik basınçlara yönelik Biyomekanik Eşiklerin izin verildiğini ortaya koyuyor. Tablo aynı zamanda kuvvetleri ve geçici temasları da gösterir, ancak bu değerler literatür çalışmalarından elde edilmiştir. "Uygulanamaz" ifadesini gösteren geçici kontaklar için veri mevcut değildir.
- Durdurma Kategorisi 0, elektriğin kesilmesiyle derhal durdurulmasıdır.
- Durdurma Kategorisi 1, tam durma elde edilene kadar kontrollü bir durdurma ve ardından güç kesilir.
- Durdurma Kategorisi 2, gücün mevcut olduğu kontrollü bir durdurma.
Bu yazımızda, hem ISO 10218 bölüm 1 hem de 2'de güvenlik fonksiyonları için Fonksiyonel Güvenlik Performans Seviyeleri belirtilmiştir. Fonksiyonel güvenlik, ISO 13849 ve IEC 62061 kapsamındadır. ISO 13849 kapsamında, tehlikeli bir arızanın meydana gelme olasılığı saat başına (PFHD), daha küçük veya daha düşük PFHd değerleri daha iyi güvenlik performansı anlamına gelir.
RİSK DEĞERLENDİRME SÜRECİNDE RİSK TAHMİNİNİN BELİRLENMESİNDE DİKKAT EDİLMESİ GEREKEN DİĞER HUSUSLAR:
- Zararın şiddeti
- Zararın meydana gelme olasılığı
- Tehlikeye maruz kalma (sıklık ve süre)
- Tehlikeli bir olay olasılığı
- Zararı önlemek için teknik ve insanî olanaklar.
RİSK DEĞERLENDİRMESİ FABRİKA OTOMASYONUNDA ÖZELLİKLE ROBOT UYGULAMALARINDA NEDEN KESİNLİKLE GEREKLİDİR?
Ne yazık ki sektörde yaygınlaşan ve doğru şekilde yönetilmesi gereken yanlış kanılar var:
“Cobot'lar ihtiyacınız olan tüm güvenliği sağlıyor”. Yanlış!
Cobot'lar tek başına kolaboratif değildir; yalnızca cobot uygulamaları kolaboratif olabilir. Doğru şekilde uygulandığında, kolaboratif güvenlik işlevlerine sahip robotlar, cobot güvenlik işlevlerinin doğru şekilde ayarlandığından emin olmak için bir risk değerlendirmesi ve ölçümler yapıldıktan sonra uygulamalarda güvenli bir şekilde kullanılabilir.
“Cobot size çarparsa sorun olmaz”. Yanlış!
Başa ve gözlere temas yasaktır. ISO/TS 15066'ya (RIA TR R15.606) göre temas teknik olarak uygun olsa bile, robot uygulamasından kaynaklanan bir darbe yaralanmaya ve ağrıya neden olabilir.
"Bu bir cobot, dolayısıyla robot bir şeye çarptığında sorun yaşamayacaktır". Yanlış!
Tekrarlanan çarpışmalar (darbeler) robotun zamanından önce aşınmasına neden olabilir.
Genel olarak üretim ve özel olarak robot teknolojisi nispeten güvenli olabilir; Çalışma İstatistikleri Bürosu'nun bir raporu için bu bağlantıya tıklayın!
Güvenlik ilgisini ve performansını sürdürme sorumluluğu tüm endüstrinin (robot üreticileri, entegratör ve kullanıcı) üzerindedir. Ancak bunu yıldan yıla sürekli olarak geliştirmemiz gerekiyor. Kapsamlı bir risk değerlendirmesi, imalat sektöründeki çalışanlara yönelik bu risklerin hem tanımlanmasına hem de azaltılmasına yardımcı olacak temel araçtır.
Risk değerlendirme sürecinin özünde basit bir döngü bulunuyor:
- Sınırları belirleyin
- Tehlikeleri tanımlayın
- Riskleri tahmin edin
- Riskleri ciddiyet, maruz kalma, olasılık ve önlenebilirliğe göre değerlendirin.
- Riskleri tasarım yoluyla (yerleşim düzeni, uygulama bileşenlerinin seçimi), ardından teknik araçlarla (korumalar ve güvenlik cihazı) ve son olarak idari önlemlerle (işaretler, eğitim, prosedürler ve çalışma talimatları) azaltın.
- Gerektiği kadar tekrarlayın.
Ayrıca şirketlerin üretim boyunca güvenliği artırmak için sürdürülebilir ve etkili bir risk değerlendirme süreci oluşturmaya başlamalarına yardımcı olacak kaynaklar ve araçlar mevcuttur.
Otomasyonu Geliştirme Derneği olan A3, robot güvenliği ve risk değerlendirmeleri hakkında kapsamlı bir ürün, yayın ve sınıf paketine sahiptir.
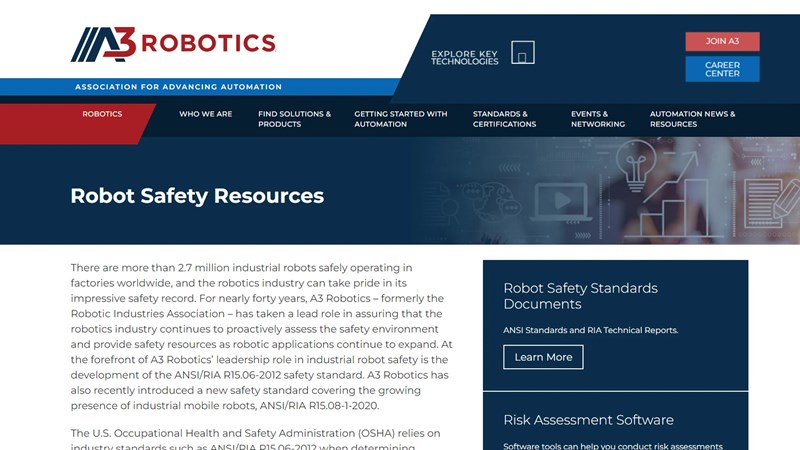

SICK Sensor Intelligence, risk değerlendirme danışmanlığı gerçekleştirir ve geniş bir donanım yelpazesine ek olarak tüm RA faaliyetlerini tanımlamak ve takip etmek için bir risk değerlendirme yazılım paketi sunar.
https://www.sick.com/us/en/catalog/products/safety/c/g568264
SICK ayrıca güvenlik cihazlarını UR'nin Polyscope geliştirme ortamına entegre etmek için UR ile çalışıyor.
https://www.universal-robots.com/about-universal-robots/news-centre/universal-robots-and-sick-announce-innovative-new-safety-solution/
TÜV Rheinland, ürün ve sistemleri test eden, denetleyen ve sertifikalandıran, güvenlik ve risk değerlendirme eğitimi veren bağımsız bir şirkettir.
https://www.tuv.com/landingpage/en/training-function-safety-cyber-security/
Bir Clarion Safety şirketi olan Machine Safety Specialists (MSS), RA yazılımı da dahil olmak üzere makine koruması, güvenlik eğitimi ve risk değerlendirmeleri konusunda uzmanlaşmış bir danışmanlık firmasıdır.
www.machinesafetyspecialists.com
Yukarıdakilere ek olarak UR, UR cobot'larında sağlanan güvenliğin ve genel olarak risk değerlendirmelerinin açıklığa kavuşturulmasına yardımcı olacak referans materyal ve kaynaklara sahiptir.
Güvenlik ve yüz yüze eğitim sınıflarıyla ilgili UR Akademi modüllerini buraya tıklayarak inceleyebilirsiniz.