Otomotiv sektöründeki robot teknolojisi kullanımı gün geçtikçe artıyor. Dünyaca ünlü araç markası Nissan Motor Company de bunlardan biri. Nissan, yaşlanan iş gücü ve verimsiz üretim süreçleri nedeniyle gereken geçici çalışanlara harcanan fazla maliyetten tasarruf etmek için Universal Robots’un UR10 cobot’u seçti.
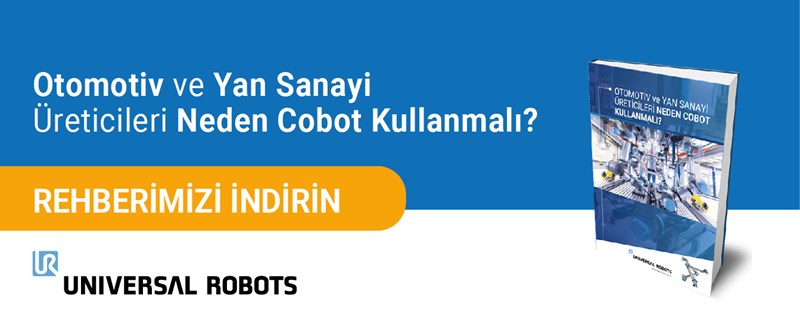
YÜKSEK 'ÇEVRİM ZAMAN' PERSONEL MALİYETLERİNİ YÜKSELTİYORDU
Motorluların yanı sıra elektrikli ve hibrid arabalar için de parçalar üreten Nissan’ın 3 bin 200 çalışanı, üretim hattı ile mühendislik departmanları arasında yakın bağlantılarla makine parçalarının işlenmesinden ve monte edilmesinden sorumluydu. Bu entegre üretim yaklaşımı, çalışanlara yeterli desteğin sağlanması ve gereken deneyimin kazandırılmasının önemini artırıyordu.
Tesis açısından bu alanda sorun yaratan bir konu, belirli bir prosesin çevrim zamanıyla ilgili olan ‘takt zamanı’ oldu. Bu süre, bazen aşılarak ek bir istihdam gerektirdiğinden Nissan’ın işçilik ve personel maliyetleri yükseliyordu. Şirket, büyük ölçekli Yokohama tesisinde üretim süreçlerini daha düzenli hale getirme ihtiyacının yanı sıra yaşlanan iş gücü ve kalifiye çalışanların kaybedilmesi gerçeğiyle karşı karşıyaydı.
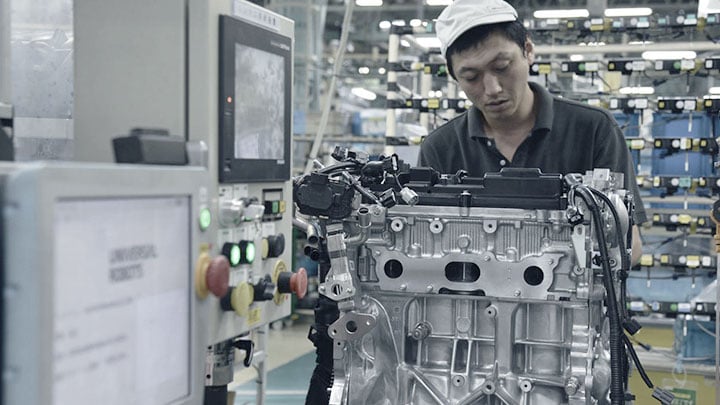
HAFİF VE KOLAY TAŞINABİLİR, GÜVENLİK ÇİTİ OLMADAN KULLANILABİLECEK COBOT'LARLA MÜKEMMEL ÇÖZÜM
Yokohama tesisinde Universal Robots’un iki adet UR10 cobot’unun devreye alınmasıyla çalışanlara farklı hatlarda değerli deneyimler kazandırmanın yanı sıra ‘takt zaman’ aşımlarını ortadan kaldırmaya yarayacak zaman da kazandırılmış oldu. Cobot’lar ilk olarak silindir kafası kam braketlerindeki somunları gevşetmek için kullanıldı. Üretim Mühendisliği Bölümü’ndeki yetkili isme göre bu iş için hafif ve kolay taşınabilir olması, 220V prizde çalışabilmesi ve güvenlik çiti olmadan kullanılabilecek özel bir robot gerekiyordu. Universal Robots’un insanla iş birliğine dayalı cobot’ları risk analizi değerlendirmesine bağlı olarak ek bir güvenlik aparatına ihtiyaç duymadan operatörlerle yan yana güvenle çalışma özelliğiyle bu iş için mükemmel çözüm oldu.
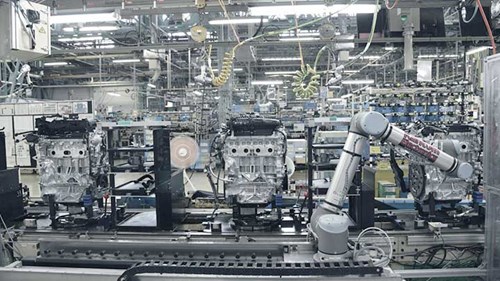
COBOT'LAR AĞIR EMME MANİFOLDU PARÇALARINI TAŞIYOR
Universal Robots’un UR10 cobot’u, motor emme manifoldlarının takılması prosesinin bir parçası olarak devreye alındı. Bu durum cobot’ların çalışanlarla iş birliği içinde çalışacağı anlamına geliyordu. UR10’un dahil olduğu çalışma, konveyör kayışları boyunca güvenlik çitleri olmadan hareket etmek ve ağırlığı 4 kg ile 6 kg arasında değişen ağır emme manifoldu parçalarını taşımayı içeriyordu.
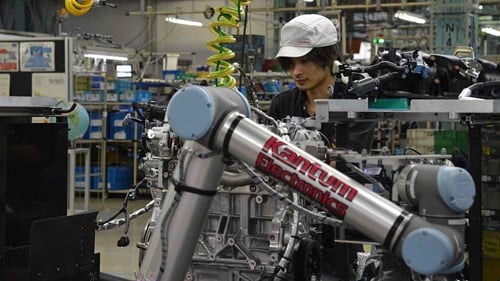
UR10'UN 10KG'LIK TAŞIMA KAPASİTESİ SEÇİMDE ETKİLİ OLDU
Nissan’ın Fabrika Motor Bölümü Ustabaşı Şefi, Universal Robots’a yönelmesiyle ilgili süreci, “Robotları seçmeden önce diğer şirketlerin robotlarıyla bir karşılaştırma yaptık, ancak tek bir robot maliyeti ve ağırlık kapasitesi avantajları nedeniyle sonunda UR10 cobot’unu seçtik. ZD prosesinde tekerleklerle hareket edebilmek avantaj sağlıyordu. Emme manifoldlarının montajı prosesi için baktığımız diğer ürünler arasında sadece UR10’un 10 kilogramlık taşıma kapasitesi bulunuyordu” diye ifade etti.
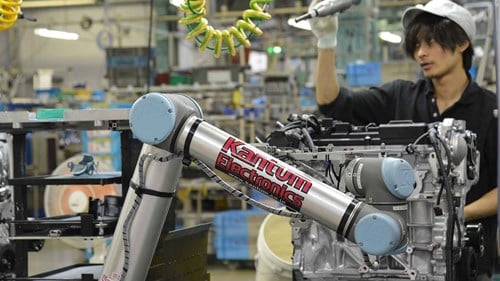
COBOT ÇALIŞANLARIN KALDIRMASI GEREKEN AĞIR YÜK MİKTARINI AZALTTI
Güvenlik ve diğer avantajları göz önüne alınarak UR10 cobot’lar kuruldu ve programlandı. Operatörler eğitilerek temel operasyonlar bir hafta içinde başladı. Kurulum sonrası programlar özenli bir şekilde ayarlandı; cobot o günden beri istikrarlı bir şekilde çalışarak şirketin takt zaman aşımı sorununu çözümledi ve personelin kaldırması gereken ağır yük miktarını azalttı.
ESNEK ÇÖZÜM SUNAN COBOT İLE ÜRETİM EKİPMANI OLUŞTURACAK
Nissan’ın Motor Bölümü Alt Bölüm Şefi, “Universal Robots cobot’unu takt zaman aşımı yaşadığımız her yere taşıyarak, sorunlara esnek çözüm sunacak üretim ekipmanı oluşturmayı düşünüyoruz” diyor ve ekliyor: “Güçlü tesis ve mühendislik olanaklarını entegre ederek küresel pilot tesis işlevini daha da derinleştireceğiz. Bu nedenle gelecekte robotların sayısını kesinlikle artıracağız”.
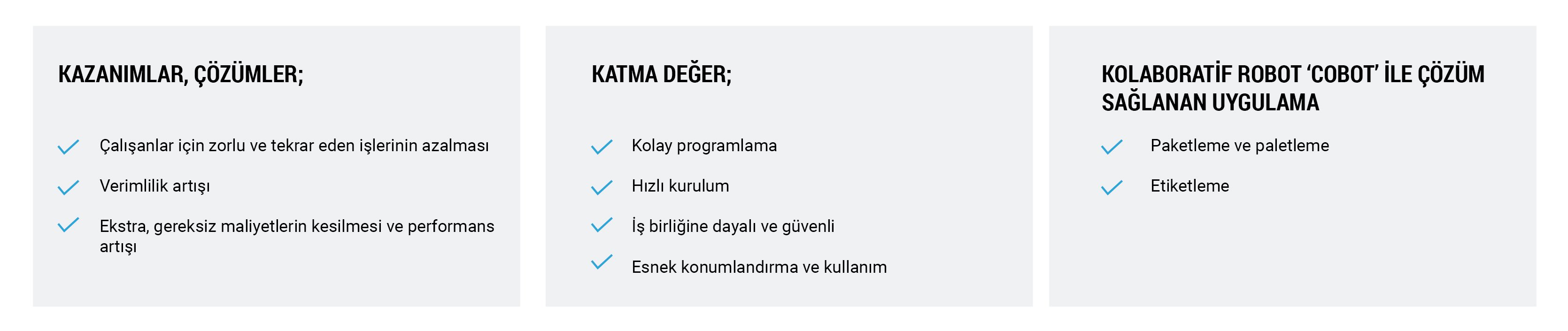